For many 3D printing enthusiasts, wax wouldn’t be their go-to material, but it has fast become the resin of choice for many jewelers, dentists, and industrial casting manufacturers.
Wax’s role in investment casting – a millenia-old metal-forming process – is actually far from new. In fact, it’s 3D printing that’s changing the wax casting landscape, with the technology bringing enhanced speed and tailorability to mold, core, and pattern-making.
So big is the business opportunity behind wax 3D printing, that it continues to be a key target market for industry leaders such as 3D Systems, Formlabs, and voxeljet. But what exactly can you make with their products? Read on for a breakdown of how the technology works, where it’s best applied, and why it’s so popular among those operating in certain niches.
Read our overview on common 3D printing materials to find out more.
How does wax casting work?
Wax 3D printing builds on techniques that have been time-tested by generations of metalworkers. In traditional investment casting, a wax pattern is coated in a refractory metal before being melted away, leaving behind a cast cavity in the shape of a desired product.
Working in a very similar fashion, wax 3D printing allows you to precisely create product molds, only rather than injection molding or carving out patterns, you can customize each one with CAD design software. This toolless patterning process is not only faster, it’s cheaper, and depending on the technology used, 3D printing can also yield several other benefits.
Which wax 3D printing process is best?
With industrial resin 3D printers, it’s possible to cure wax-based materials into intricate castings for dental models as well as pieces of jewelry that don’t require finishing – something that’s seen as a real win for jewelers. The same can be said for material jetting systems, the likes of which fire ‘inks’ onto a printer’s build platform, that are then solidified layer-by-layer.
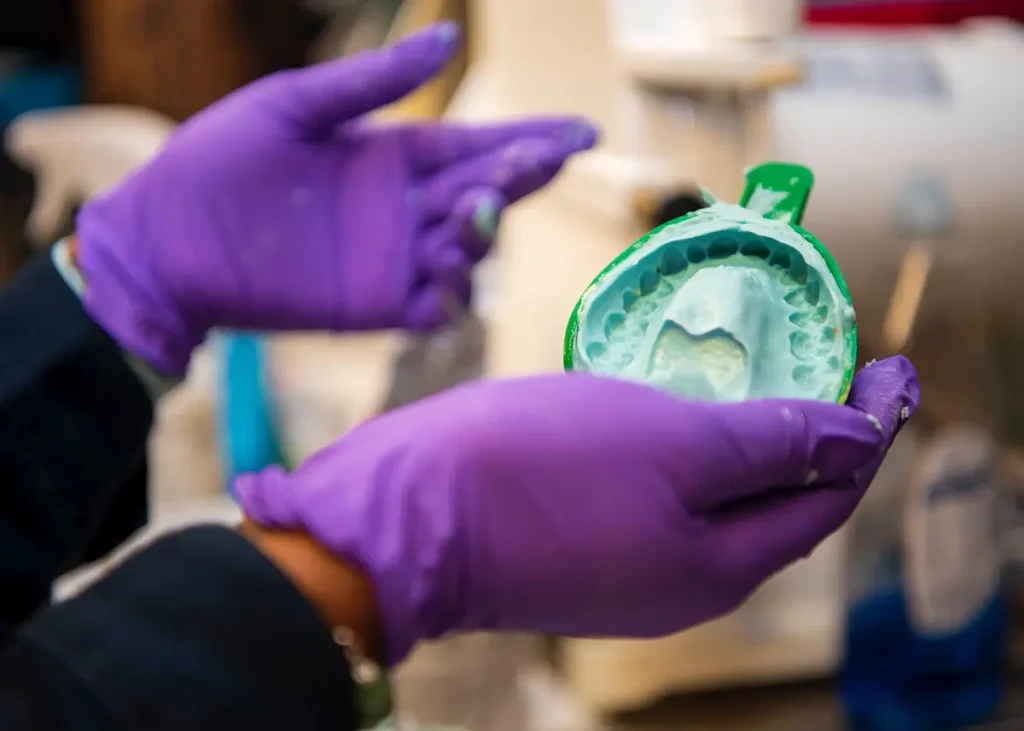
The multi-material nature of the technology means it can be used to create multi-color parts with mixed properties and functionalities. However, in order for materials to be jettable, they need to feature very specific properties. This limits the compatibility of material jetting, a process which already tends to be pricier and closed to many third-party materials.
Waxes can also be used with many FDM machines. If your system has a wax profile, that’s said to make this easier to do, but where you can, using resin often delivers best results.
The success of your wax manufacturing efforts are also likely to depend on which material you opt for. When it comes to choosing one, you should consider how long it will take to melt, how much ash it’ll produce, and its level of shrinkage post-printing. Each of these factors can impact quality and the amount of maintenance you need to perform on your 3D printer.
Where is the technology utilized?
Compared to metal or plastic additive manufacturing, wax 3D printing is more niche. One of the technology’s most popular applications is jewelry-making. As alluded to earlier, wax 3D printing is utilized more to create molds rather than jewelry itself. It is possible to 3D print custom rings or bracelets, but binder jetting is a better suited process for doing so.
It’s as an alternative to traditional casting manufacture that the technology really shines. It’s faster and fully customizable, allowing jewelry makers to get creative with designs and iterate more often. What’s more, many industrial machines are built to fit existing workflows, so they can easily be integrated to churn out batches of flawless wax patterns for same-day casting.
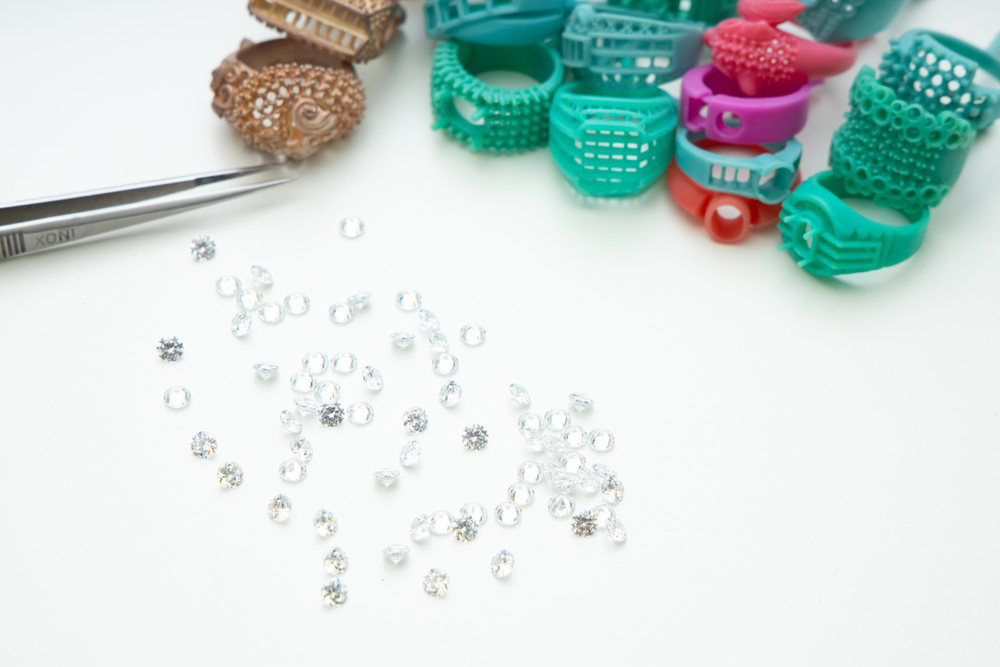
Take 3D Systems’ MJP Series – these large-format, high productivity 3D printers are capable of creating thousands of pure wax castings each month. At the smaller end of the application scale, Formlabs also offers castable wax resin for its desktop machines.
Not just designed to cater for jewelers’ needs, the material’s blend of strength and stiffness is said to make it ideal for producing ultrafine, thin structures ranging from product prototypes to dental crowns and bridges. Voxeljet also markets its VX200 and VX1000 machines as ways of creating uniquely high resolution castings with “no limits in geometric complexity.”
Of course, we’re talking about big industrial units across the board here, but this is where wax 3D printing’s most convincing business case lies. If you’re looking to make custom jewelry in lower volumes, FDM may make sense as an alternative, but even then resulting castings will have to undergo post-processing to remove layer lines prior to usage.
What next for wax 3D printing?
They may not be used as widely as metals or polymers, but waxes continue to be central to 3D printing’s viability as means of modernizing investment casting. Mostly, the technology is confined to this space due to material restrictions. Issues like viscosity (fluidity) and ultimate product strength often makes waxes unattractive in other applications.
However, that’s not to say the technology is standing still, or to take anything away from its casting-making credentials. Metal casting remains a lucrative, rapidly growing market, and with a number of industry leaders still building out their wax 3D printing offerings, it’s clearly seen as a lucrative area where these can take a larger slice of the pie.