One of the many inspiring things about the 3D printing industry is that it’s packed with people who invent just because they can. Much of the time, makers and researchers innovate without a specific business goal in mind, and instead work towards addressing a wider issue.
In the past, these efforts have focused on making 3D printing accessible via the development of low-cost, open-material extrusion machines. But, as the technology continues to advance, charitable innovators have begun applying it in new humanitarian areas, ranging from the customization of prosthetics, to the erection of housing in deprived neighborhoods.
It’s often said that 3D printing, an additive process that only uses the exact amount of material required for each build, also does environmental good. However, this idea has always been hamstrung by the technology’s reliance on petroleum-based polymers or mined metals – both of which are sourced unsustainably.
You’d be forgiven for thinking there are very few alternatives, but wood 3D printing is really starting to gain traction in certain applications. Generally made from recycled goods, sawdust, or plain old endlessly renewable wood, these feedstocks tick the right environmental boxes, but how do they stack up when it comes to manufacturing actual products?
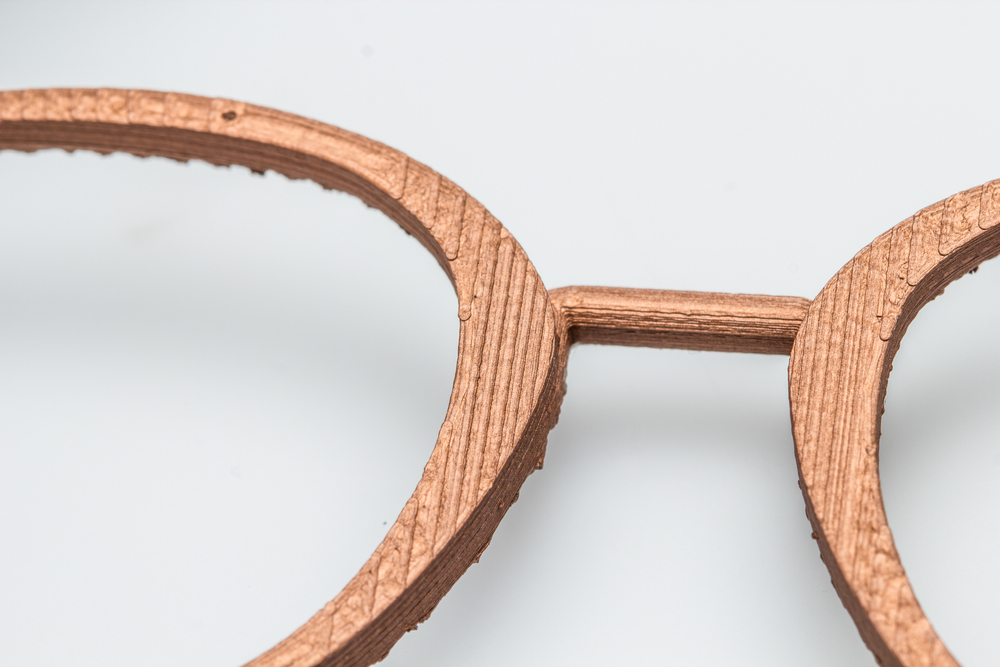
Read on to get a deeper understanding of how the technology is coming along, what you can actually make, and where it may head in the years to come.
Want to find out more about common 3D printing materials? Check out our overview!
Is wood 3D printing really possible?
Yes! Obviously, it remains a long way from widespread adoption, but wood 3D printing is already showing great potential, both in R&D and fledgling end-use applications.
Over the last few years, researchers at the University of Freiburg have taken significant strides in their efforts to develop a 3D printing material made from lignin, an organic, plant-sourced polymer. A team at MIT has also experimented with 3D bioprinting wood cells into futuristic furniture items, and thanks to the efforts of Forust, the technology now looks set to enter the mainstream market.
Using the binder jet process of parent company Desktop Metal, Forust has come up with a way of using a material made up of manufacturers’ sawdust and lignin leftovers, to create custom household goods. This includes everything from luxury interior design items with textures that mimic those of real oak, teak, or walnut.
Similarly, sustainable architecture specialist Aectual has developed a means of creating furniture from recycled drink cartons. Unlike Forust, however, the firm mounts its 3D printers to robotic arms, programmed by an algorithm that cuts CO2 emissions with every job.
What can you 3D print from wood?
So, having looked at wood 3D printing from a technological perspective, it’s worth asking: what can you actually buy? This is where the marketing methods of Desktop Metal and Aectual differ.
Since acquiring Forust in 2020, Desktop Metal has marketed wood 3D printing as an online service for those working in automotive, architecture, and consumer goods to create part batches on-demand. Now, such manufacturers can also buy their own Forust version of Desktop Metal’s Shop System, install it in-house, and make what they’d like.
This approach is great for developing applications with customers, (and understandable given the emerging nature of the technology), but it does reflect a general lack of established use cases for it. By contrast, Aectual will sell you anything from a 3D printed vase to an entire room divider today and deliver it to you in a matter of weeks.
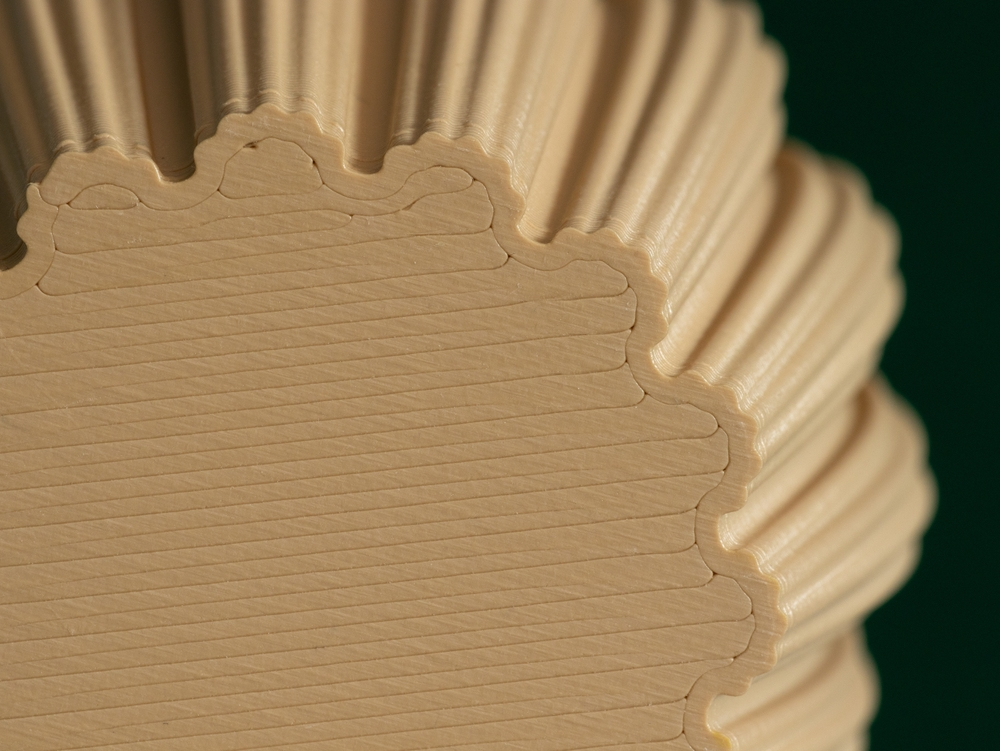
At a more affordable level, wood is also being turned into FDM filaments. However, these tend to be reinforced by PLA, taking away from their sustainable credentials. For the time being, if you’ve got ambitions of 3D printing viable, 100% wooden items, you’ll have to either invest in an industrial unit or wait for researchers to come up with something more accessible!
How does wood fabrication stack up?
With 3D printed furniture having hit the market, it’s clear that wood is not just making great strides in research labs, and it’s becoming more than an additive manufacturing novelty.
Whether it can carve itself a niche in architecture or not, time will only tell. With Aectual’s cheapest furniture items being €494, they’re definitely premium products for early adopters, but there’s no doubting their eco-credentials.
With polymers accounting for 58% of the 3D printing market, pressure is mounting for greener material alternatives. This shift, reflected in the foundation of sustainability organizations like the AMGTA and deeper life cycle analyses (LCAs) than ever being carried out by 6K Additive and more, is creating a gap where bio-alternatives such as wood can flourish.
That’s not to say we’re anywhere near seeing the end of plastic 3D printing. But as is so often the case with additive manufacturing, wood is a new material showing potential in some very specific applications, and who’s to say where this architectural niche will head next?
I don’t think the title of your article matches the content lol. Just kidding, mainly because I had some doubts after reading the article.