Messe Frankfurt – home of Formnext 2024.
3D Mag announced its full launch ahead of Formnext 2024 – the latest iteration of the 3D printing industry’s leading trade show. Our team covered the event live from the showfloor. Here are our impressions of the latest, most innovative technologies unveiled at the event.
It has been three long years since I reported on Formnext in-person and it was clear from the showfloor that the technologies behind 3D printing have since come on leaps and bounds. While there was also evidence of recent industry turbulence, with frontrunners Desktop Metal and Nexa 3D dialing back their presence, there was still plenty of innovation on-display.
This year, there seemed to be a greater application focus than ever before, with technologies boasting a clear return on investment (ROI) featuring even higher on the agenda.
There were also signs of a continuing boom in desktop 3D printing adoption. Bambu Lab’s booth – alongside Prusa’s (with its ultra-loyal fanbase) – proved popular throughout. As such, the maker space seems to be flourishing in spite of a harsh economic climate. We’ll reserve any hot takes for our upcoming Formnext ‘industry insider’ feature, but hopefully that gives you a flavor of the atmosphere at the show.
Now, moving onto launches. This year’s Formnext was packed with a plethora of new 3D printing systems, materials, and technologies. Let’s look at some of those who shone brightest!
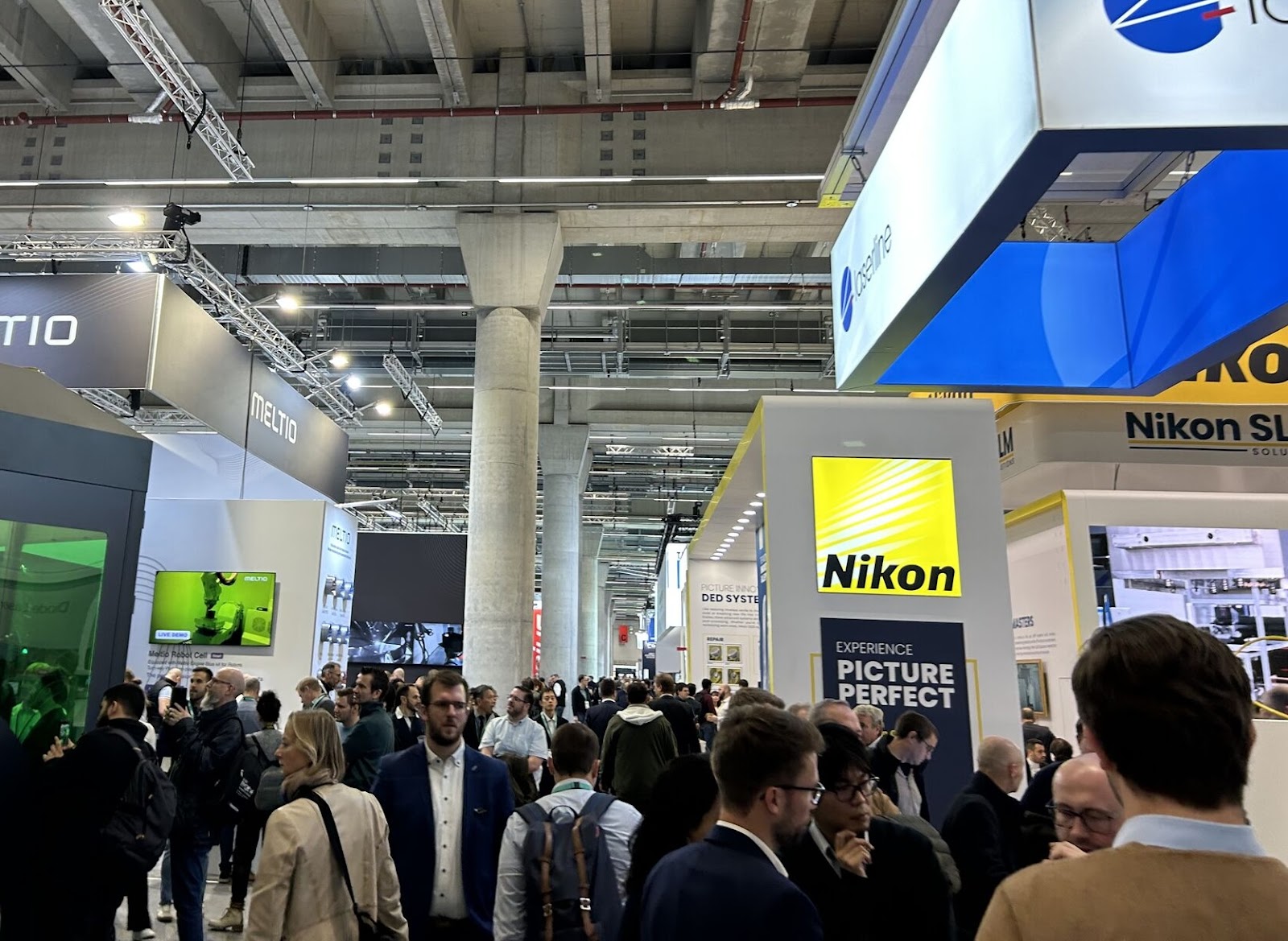
The Formnext 2024 tradeshow floor featuring Nikon, Meltio, and more.
EOS, Lynxter & more launch new 3D printers
EOS made one of the highest profile additions in the industrial 3D printing space, with the launch of its P3 NEXT system. Building on the design of its predecessor – the P396 – EOS’ latest polymer 3D printer boasts 50% higher productivity and a 30% lower cost of ownership.
While the system features the same laser and recoater as before, it has been fitted with several upgrades to make it a true end-to-end production package. When it starts shipping next year, for instance, the P3 NEXT will come with a nitrogen-fed cabinet. This allows for materials to be ‘hot-swapped’ so users don’t have to wait for waste to cool between production runs.
EOS Polymer Application Specialist Jean Cunha told me how this would “improve efficiency and reduce part cost” significantly. Particularly for those operating in dental, medical, and service bureaus – areas where it already has a large customer base.
EOS’ latest polymer 3D printer boasts 50% higher productivity and a 30% lower cost of ownership.
Next up, Lynxter impressed with its new thermoplastic 3D printer, the S300X – FIL11. The French manufacturer has made a name for itself with IDEX technology – a twin extrusion 3D printing process, where printheads can deposit filament simultaneously or independently.
According to Adeline Aubin, Lynxter’s international head of commercial development, their previous big modular silicone and ceramic machines still meet a market need. But Lynxter also continues to see “high-demand for technical filaments” – and the S300X FILL 11, with its PEKK-compatible heated chamber and built-in material dryer, can be seen as a proactive response to this.
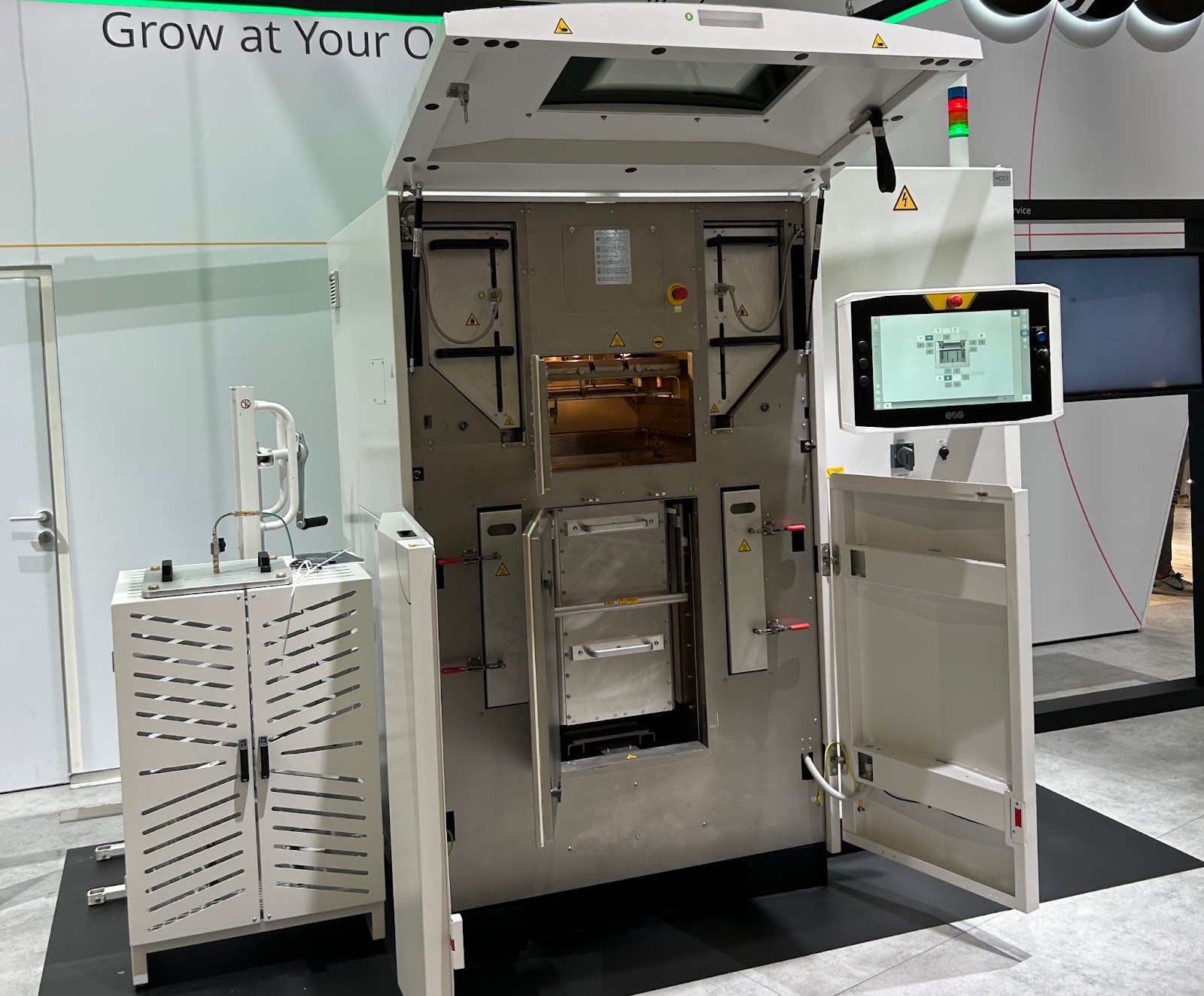
The EOS S300X FILL 11 3D printer at Formnext 2024.
Another of the major players at the event, Nano Dimension, introduced the Exa 250vx, an ultra-fine digital light processing (DLP) machine. Compared to previous generation Giga and Tera systems (built using its acquisition NanoFabrica’s technology), Exa 3D printers can create 10-micron layer part batches with 50 x 50 stitching – a big jump on the 2 x 6 offered before.
At the booth, Adir Zilber told me how the unit’s high viscosity resin compatibility also lifts print speed, while its ability to work with any 385nm curable material leaves it open to innovation. In practice, the Exa 250vx is expected to thrive in any application where extremely high accuracy is key – whether it be in medical, microoptics, or microfiber manufacturing.
The Eva 250vx digital light processing (DLP) 3D printer is expected to thrive in any application where extremely high accuracy is key.
Then there’s Q. Big3D. The company exhibited with a suitably huge booth for exhibiting its oversize polymer 3D printer – the XXXL. Fused granulate fabrication (FGF) pellet 3D printing has been around for some time, but Q. Big3D’s variable FGF technology is designed to create even finer surfaces at scale, while remaining much faster than traditional FDM.
To demonstrate VFGF’s potential, the firm exhibited huge aerospace and automotive prints. Q. Big3D sales manager Oliver Friz explained that it’s perfect for making “all big parts that would be impossible to produce otherwise,” adding that “the possibilities are limitless.”
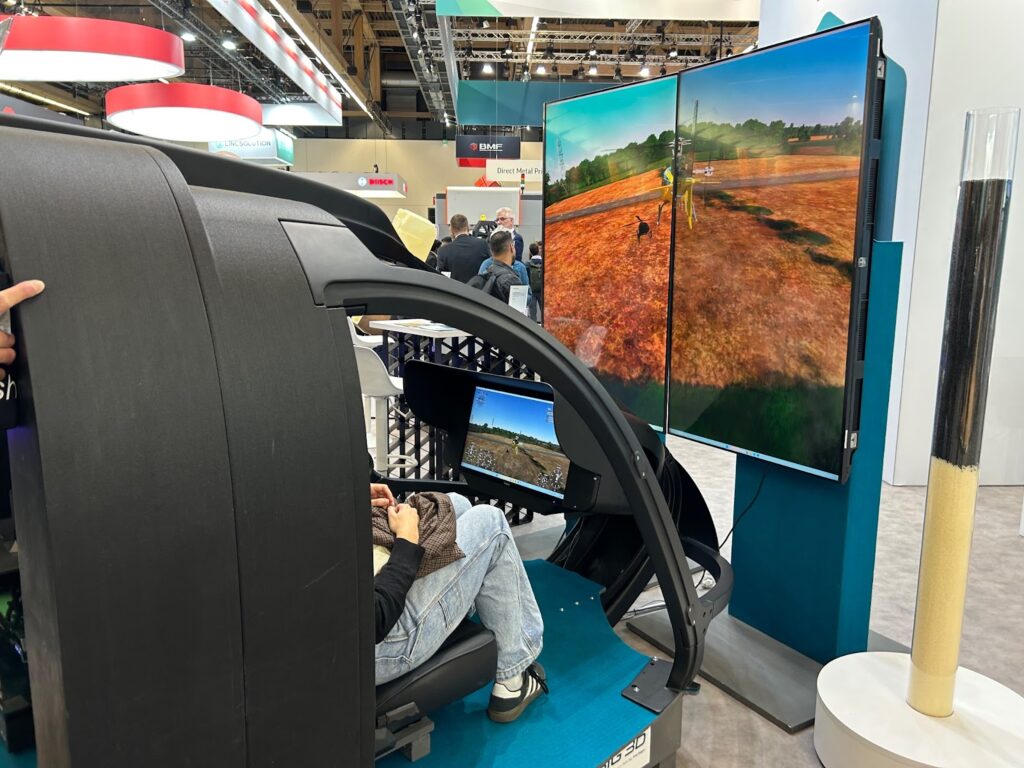
A 3D printed helicopter cockpit installed in Q. Big3D’s booth at Formnext 2024.
Renishaw, WASP & Solukon unveil technologies
British engineering stalwart Renishaw teased announcements ahead of Formnext. But rather than additions to its RenAM metal 3D printing product line, it unveiled two new technologies.
The first of these, ‘Tempus,’ allows powder to be reloaded without deactivating a 3D printer’s laser. This enables RenAM machines to print over two times faster than four-laser predecessors and at four times the pace of those with single-lasers. Renishaw also introduced ‘swimlanes’ that ensure each laser has a dedicated lane, preventing any risk of intersection.
Tempus allows powder to be reloaded without deactivating a 3D printer’s laser. This enables RenAM machines to print over two times faster than four-laser predecessors.
Regional Sales Manager Jose Diaz explained how “the market is looking for Industry 4.0,” and that Renishaw is responding to this demand with consistent upgrades. In particular, he highlighted how its cloud-based control software is bringing this ambition a step closer to reality, combining 3D printers and traditional technologies in the same singular digital thread.
With Renishaw spending 15-20% of post-tax profit on R&D, he added that “the next step is enhancing the upload of material onto the build plate,” a workflow step ripe for optimization.
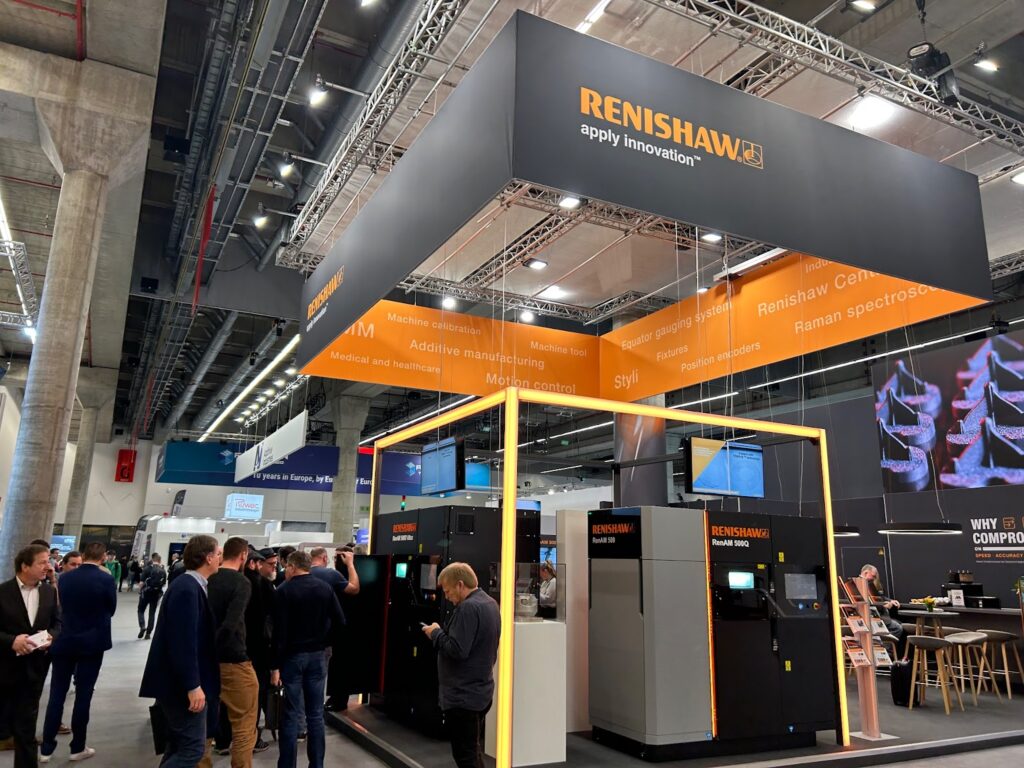
Renishaw’s booth – complete with RenAM 3D printers – at Formnext 2024.
WASP
Perhaps best known for its construction 3D printing exploits, WASP also sprung something of a surprise, by introducing a new industrial nozzle. Marketed as a ‘technical modification’ of its existing extruder, the device was mounted to a robotic arm at the company’s booth.
Working with robotics specialist CEREBRO, WASP has developed a new way of mechanizing its liquid deposition modeling (LDM) and DLP printheads. Users can even deploy an app to control robotic arms and 3D print custom geometries on-demand. The idea being that adopters can either try different materials or create end-products using multiple printheads.
Solukon
On the post-processing front, Solukon was debuting a massive new de-powdering system: the SFM-AT-1500-S. Capable of shaking excess material from parts weighing up to 2,100 kilos or 600 x 600 x 1,500 mm in size, the machine operates at a hugely impressive scale.
Solukon’s new system – which de-powdered an entire rocket chamber at the show – operates at a hugely impressive scale.
According to process development engineer Moritz Warnck, “the industry is trending towards bigger and bigger” parts, making Solukon’s latest system the ideal solution. Relatively small for its capacity, the machine rotates, vibrates, and washes powder with the help of a software that automatically senses where material could be lodged and takes mere hours to shake it free.
Ready for deployment out of the box, Warnck added that the SFM-AT-1500-S is as close to “plug and play” as you’ll get using this kind of technology. And its potential applications were there for all to see, with the machine de-powdering an entire rocket chamber at the show.
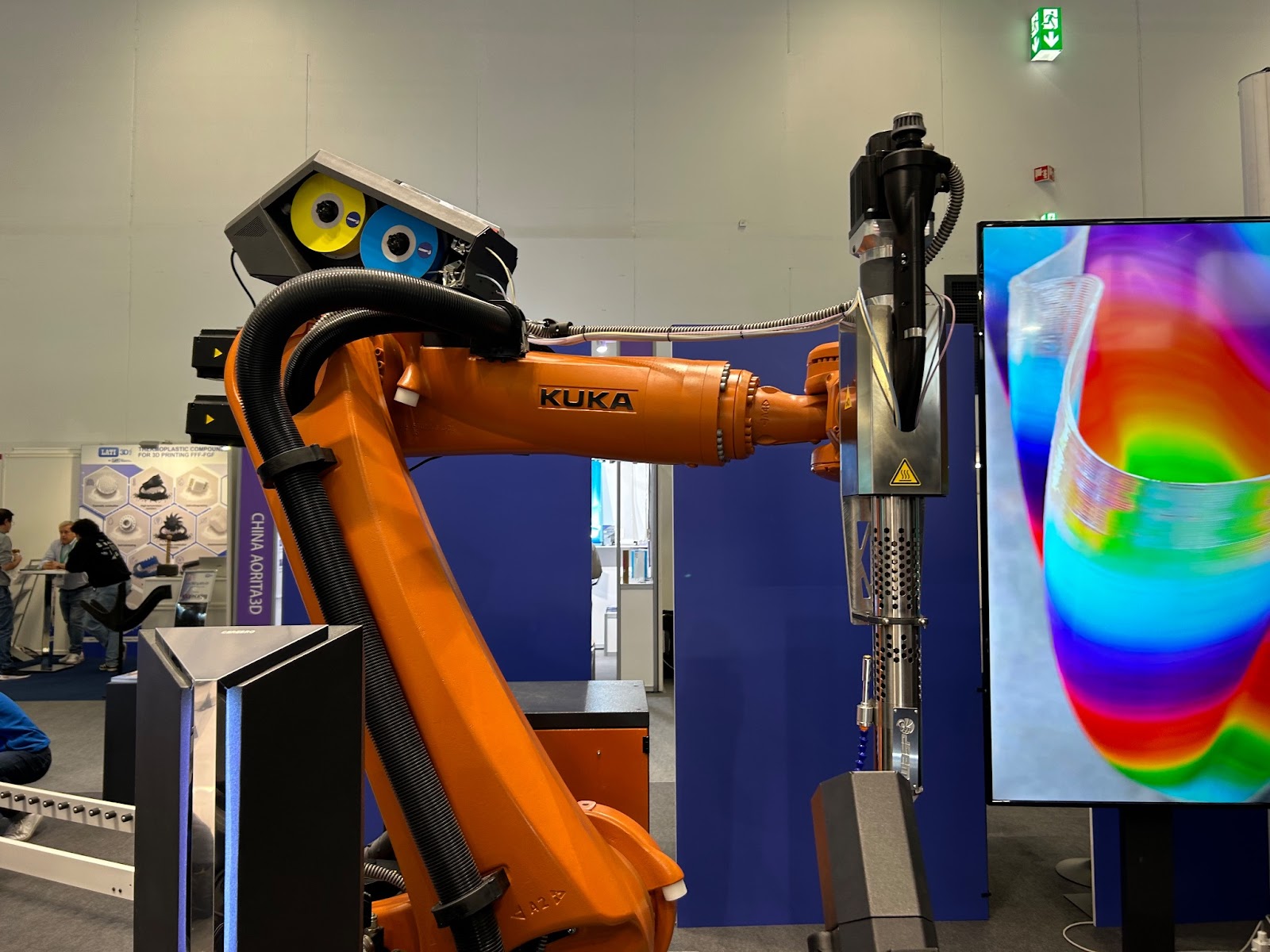
A robotic arm fitted with WASP’s new adaptable 3D printing printhead.
New materials from Henkel, Ceratizit & Carbon
Henkel
Chemical & adhesive specialist Henkel deployed its Loctite team to Formnext, so they could show off its latest 3D printing resins. ‘3D IND 684’ is an end-use material free from TPO, a harmful substance being clamped down upon at a wider level by European regulations.
Loctite’s Sam Ball put it nicely when he said “sometimes regulation drives change,” and when manufacturers are looking for low-cost, compliant parts, Henkel’s test data transparency “gives them the confidence of knowing what they’re going to get.”
As well as emphasizing Henkel’s expertise in this area, Ball showed me the all-new autoclave sterilizable ‘MED 3394.’ Medical devices are subject to repetitive sterilization, making them prone to deterioration. Henkel’s new resin counters this issue, making it perfect for the small batch manufacturing of R&D test arrays and biofluidic devices.
Henkel’s new resin withstands repeat sterilization, making it better suited to demanding medical applications.
Ceratizit
Metal manufacturing specialist Ceratizit also made its debut at this year’s event. During the show, I got the full booth tour, which included a look at wear and cutting-grade metal 3D printed parts made with micro-extrusion, fused filament fabrication (FFF), and binder jetting.
Interestingly, I was told that Ceratizit’s in-house filaments are so strong and versatile, parts made from them can literally be jumped up and down upon without suffering damage. FFF-3D printed objects, meanwhile, can be machined, turned, and drilled in a green state, allowing fine details to be added before sintering (by then, it’s much harder to achieve!)
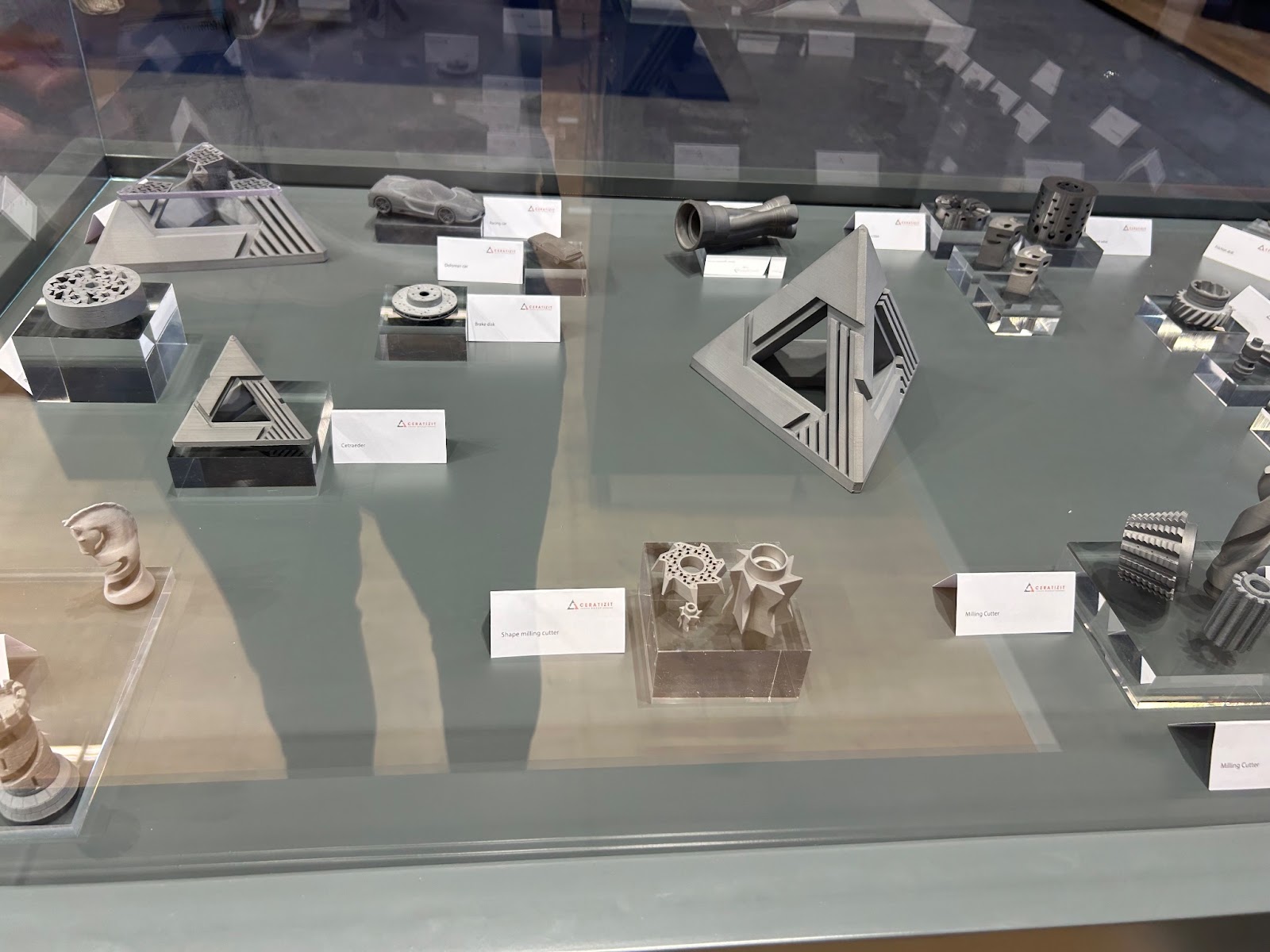
Parts 3D printed from Ceratizit’s materials – which were making their Formnext debuts.
Carbon
Lastly, Carbon chose to introduce its first single-part, dual-cure elastomer. Carbon was already known for the 3D printing of padding used inside helmets, saddles, and more, but its new EPU Pro material can be programmed to elicit entirely different responses from 3D printed lattices. This promises to take material fine-tuning and efficiency to a whole new level.
Being a single-part resin, it’s also much more eco-friendly as parts aren’t washed in solvents, processing requires fewer chemicals, and unused resin can be redeployed after a print finishes. Keep an eye out for our full interview piece with Carbon’s Gary Miller for more details!
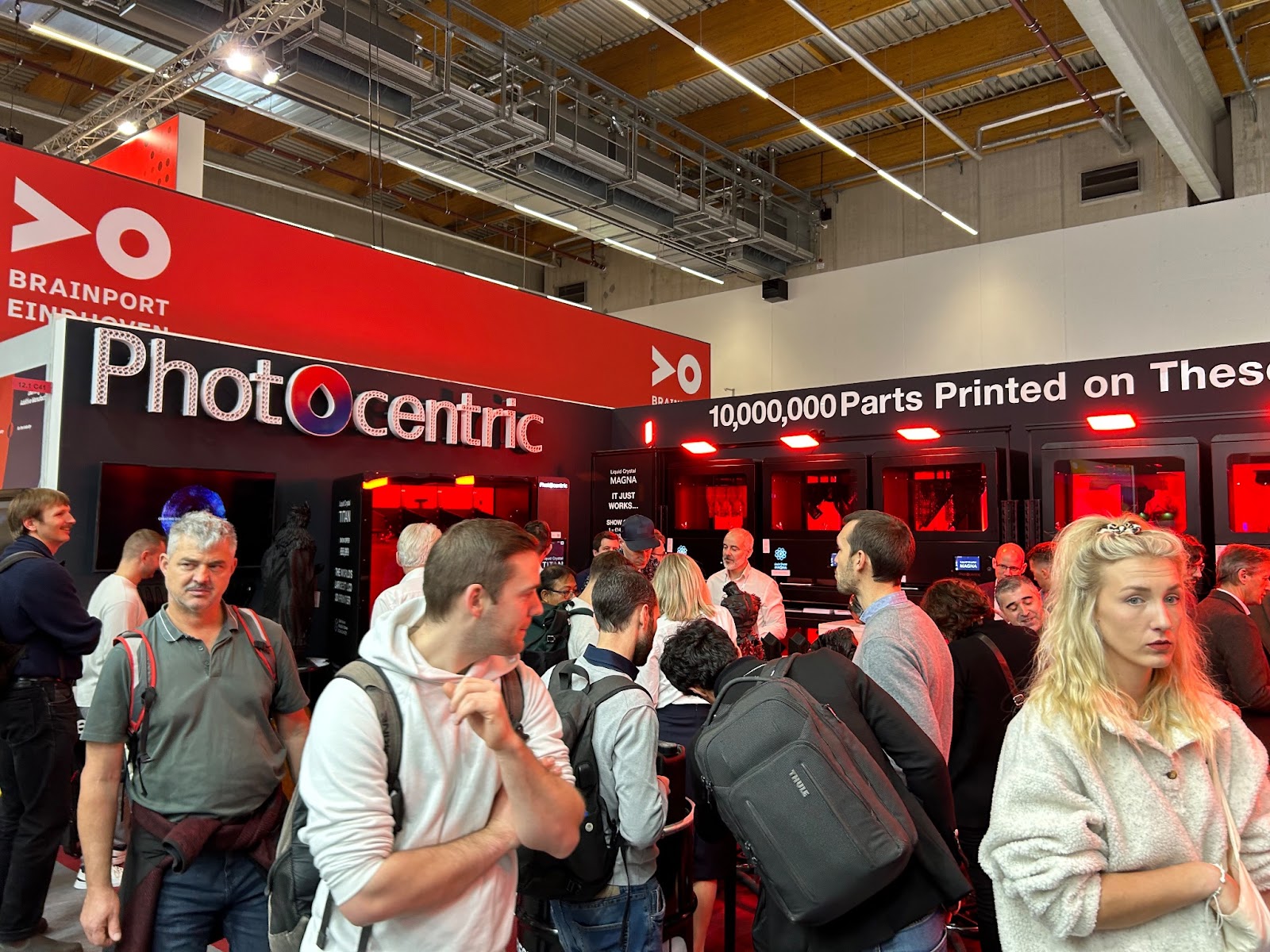
Photocentric’s ‘JENI’ automated 3D printing system.
Honorable mentions
So, that covers our top picks from the show. But what else caught our eye? Photocentric introduced a fully-automated 3D printing workflow. Though Formnext has featured many robot arm-equipped systems before, ‘JENI’ stands out for being completely modular.
Not just a bunch of resin 3D printers strapped together, this impressive workflow combines printing, curing, and post-processing technologies into scalable modules. This allows users to customize their workflow to specific applications and expand capacity (into the millions) as required. Only after parts were fully ready to go, were they removed with robotic arms.
Photocentric’s JENI system served as a visually impressive reminder that 3D printing automation remains in high demand.
I also stopped by to talk with Bambu Lab, which had an appropriately large, colorful booth at this year’s show. While the company declined to speak ‘on the record,’ or give any sneak peaks into the new 3D printer it plans to launch next year, it did commit to continuing to serve makers and new adopters – a strategy that has worked wonders for its appeal in recent times.
Our key takeaways
- Application-focus is the order of the day: Manufacturers are marketing 3D printers more around practical use cases than underlying technologies
- Material innovation continues to unlock fresh avenues for 3D printing
- Desktop 3D printing is booming and Formnext is becoming an increasingly popular meeting point for makers and SMEs alike
Stay tuned, there’s plenty more 3D Mag coverage from Formnext 2024 still to come.
All images provided by 3D Mag.