Let’s journey back in time to January 9, 2024: Industry experts from across the globe have descended upon Las Vegas to see the world’s leading technology showcase, CES.
Within seconds of walking through the doors of the Vegas Convention Center, attendees are surrounded by everything from AI-powered smartphones to EVs. After wandering the showfloor for a bit, many stumble across an area filled with red and black cushioned seating. Initially, it seems a little low-tech compared to all the advanced gadgets and gizmos around it.
But hold up! It turns out they’ve actually been 3D-printed by architecture specialist Aectual from upcycled Lenovo e-waste. Debuted at Lenovo Tech World, these little seats are just the latest example of furniture 3D printing, a movement that has gathered pace in recent years.
Whether it be in the creation of vases, chairs, walls, or buildings, the technology continues to yield proof-of-concepts with the potential to change how homes are made. In fact, with many now 3D printing household goods at their desktops, this revolution is already taking hold.
Futuristic-looking furniture and infrastructure made with 3D technologies continue to drive sustainability and innovation.
But what opportunities does the technology present in terms of design and preserving natural resources? According to Sherri Monroe, Executive Director of the Additive Manufacturing Green Trade Association (AMGTA), “3D printing is clearly more sustainable” than current practices.
“There’s no question about it, used as intended, it should be definitely more resource efficient when it comes to energy, source material, and waste,” she explained. “It’s not just about production either, it’s about iterative design, not having to produce huge quantities for things to become economic, and reducing overproduction.”
With the likes of Aectual, Desktop Metal subsidiary Forust, and UltiMaker taking the technology from workshops into retail spaces and inside peoples’ homes, it’s also gaining a commercial dimension. To get an idea of where this emerging market is headed, we’ve spoken with its early leaders about their technologies and ambitions for the future of furniture 3D printing.
Already familiar with the technology? Feel free to skip ahead to these juicy insights. But if you’re new to the field, stick around and read the next section for a full breakdown.
How does furniture 3D printing work
If you’re new to 3D printing, you’re probably wondering how exactly it can be used to create furniture. Broadly, it depends on the application, but there are plenty of ways of doing so.
Forust has come up with a method of binder jetting everything from lampshades to car interiors using ‘Forustwood’ – a recycled sawdust and bio-epoxy resin. In practice, its technology works by spreading this material across the build chamber of a Desktop Metal Shop System, where it’s selectively fused into desired shapes with a biodegradable binder.
With wood 3D printing, it’s now possible to customize design features, and redesign interiors with even greater freedom.
Aectual has taken a different approach, building its business around robot arm-mounted fused deposition modeling (FDM) 3D printers, capable of creating vast interior decorations. They do so by melting and layering material into complex shapes. This feedstock could come from anywhere – even scrap parts or disused drink cartons. Customers need only send their plastics to Aectual, which shreds this into a reusable 3D printing material with zero waste.
Elsewhere, the likes of COBOD, CyBe Construction, and WASP have also begun erecting entire buildings in a similar layer-by-layer manner, albeit from concrete substitutes.
If you’re a maker, you can even desktop 3D-print vases and lampshades at home using UltiMaker Cura. With the program’s Spiralize Outer Layers mode (aka Vase Mode) creating low-infill aesthetic prints is fast, simple, and pretty fun!
Depending on who you ask, they’ll likely say one of these technologies is better than the others. Desktop Metal CMO Sarah Webster claims “nothing really compares to binder jetting” in terms of sheer speed. Aectual’s Creative Director Hedwig Heinsman says it has opened “a lot of opportunities to 3D-print interiors from waste” with its proprietary extrusion technology.
In reality, each has its strong suits and is equipped to tackle some use cases better than others. Let’s take a look at the latest applications – with a sprinkling of exclusive insider insights.
Revolutionizing interior design
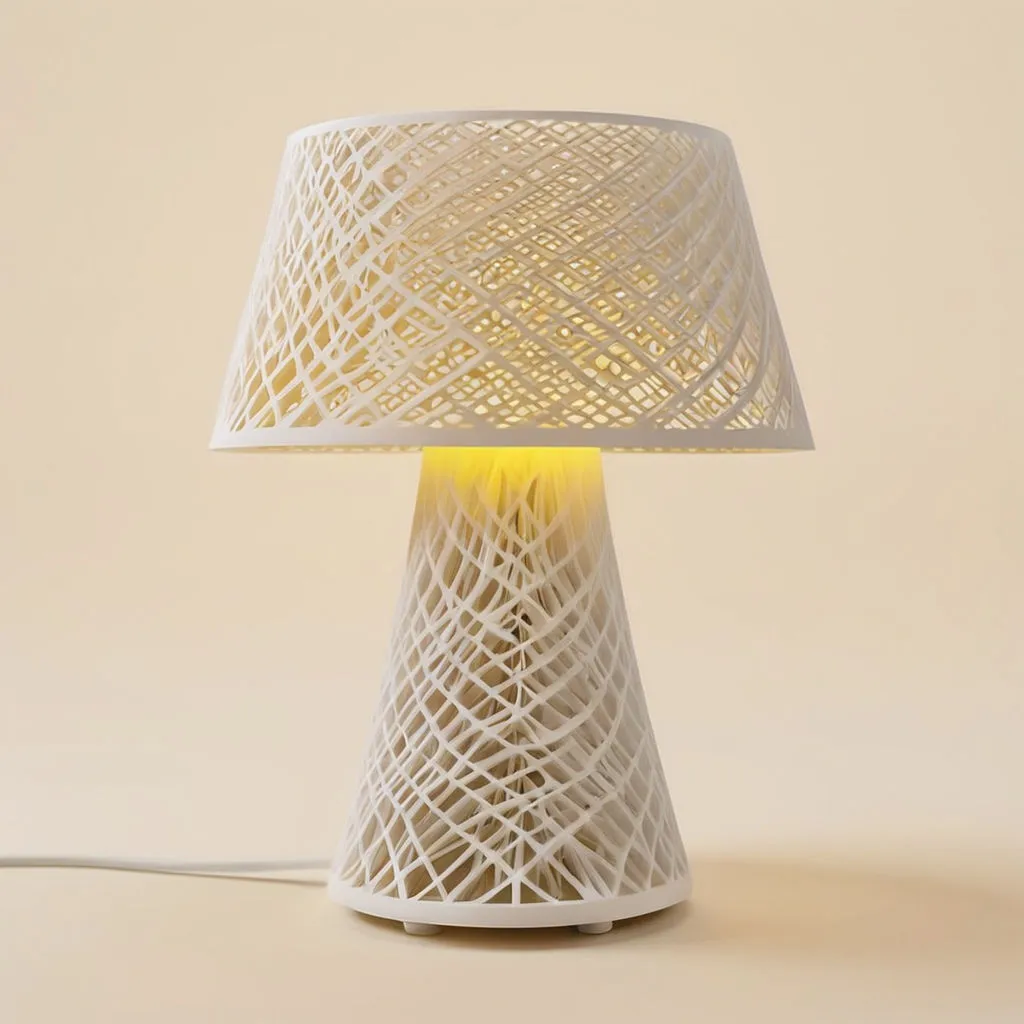
Interestingly, Forust, Aectual, and UltiMaker have each taken different approaches to marketing their furniture 3D printing technologies.
Following its acquisition by Desktop Metal in October 2020, Forust initially launched an online store, where customers could buy ready-made 3D-printed home goods such as bowls and desk tidies. Since then, it has repositioned itself. Clients can still order custom wooden parts directly, but with the launch of the Forust Shop System, they can also create them in-house.
WIth Forust technology, HagenHinderdael designers have already 3D-printed funky looking ‘cocoon’ lamps, which can be sat around the home or suspended from the ceiling. Webster says Forust technology could yet have further applications in this area, as it “brings a lot of desirable properties to lighting fixtures,” and is a “particularly good fit for creating exotic shapes.”
Aectual markets an entire range of pre-designed panels, plant pots, and more, which it 3D prints and sends to clientele.
On the Aectual store, meanwhile, you can still buy everything from 3D-printed planters to acoustic panels and hanging screens that help decorators transform interiors. According to Heinsman, the latter could be particularly useful for retailers that regularly re-fit stores.
“Let’s say after three years a store needs to change. We take back their goods and shred them into small pieces that can be reused up to ten times,” said Heinsman. “You can also combine ‘smart features’ with aesthetics to give them a level of functionality – so you can sit on them, put plants on them, or integrate lighting.”
On the software front, UltiMaker Cura is also open to the users of any FDM 3D printer to download and use, whether for regular slicing or creating aesthetic prints like vases. Interestingly, Cura Product Manager Mariska Maas gives all the credit for Vase Mode to the platform’s maker users, who uncovered the setting and continue to innovate with it.
“Cura gets contributions from community members all over the world,” explained Maas. “It was one of them, Joris van Tubergan, who introduced the Spiralize Outer Layers setting. If you want something quickly, where wall size doesn’t matter, ‘Vase Mode’ is obviously the way to go. I’m super happy we’re open-source and have people working together, troubleshooting together.”
Ready for a “single big jump”?
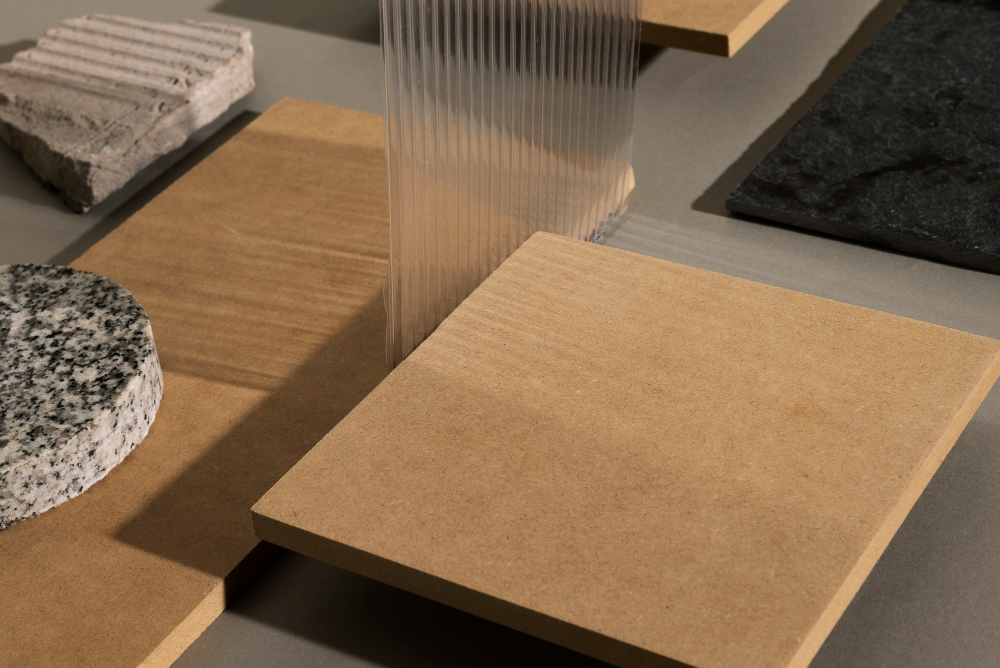
Given all the benefits of 3D printing, you may well be asking yourself: ‘Why are furniture stores sticking to painstaking traditional manufacturing rather than going digital?’
One area where the technology remains under development is ‘infiltration,’ says Webster. Put simply, this is the process of closing print surfaces to improve strength and avoid contamination.
Desktop Metal has tried many different ways of optimizing the process, but she says this hard work is now starting to bear fruit. At Carnegie Mellon, for example, researchers have managed to binder jet bio-resin into infiltrated aesthetic parts that meet industry strength standards.
Eco-friendly 3D printing research is still ongoing, but the technology is already considered more sustainable than traditional manufacturing.
“But regional wood sources also tend to have different characteristics and therefore require different processing parameters that must be developed,” caveated Webster. “Likewise, infiltration techniques and materials tend to be specific to an application.”
Infiltration raises another issue: Certification. As many countries (and even different US states) have their own regulations setting product standards, it’s tricky for those with varying 3D printing processes to disrupt the mainstream. While Heinsman also sees regulation as a hurdle to wider adoption, she believes further R&D and data gathering can help overcome this.
“We have a lot of data on what we do,” said Heinsman. “But to ensure that we meet certain standards, we’d have to run every new product that we make through all these tests again. Then there’s developing materials, I think there’s still a lot to discover there.”
As head of the AMGTA (a group that counts Desktop Metal as a founding member), Monroe is uniquely well-placed to forecast sustainable infrastructure’s future. She says a breakthrough application could yet see 3D printing speed through these roadblocks, and make a “single big jump” similar to that seen in EVs, where the Toyota Prius laid the ground for Tesla.
Forecasting further innovation
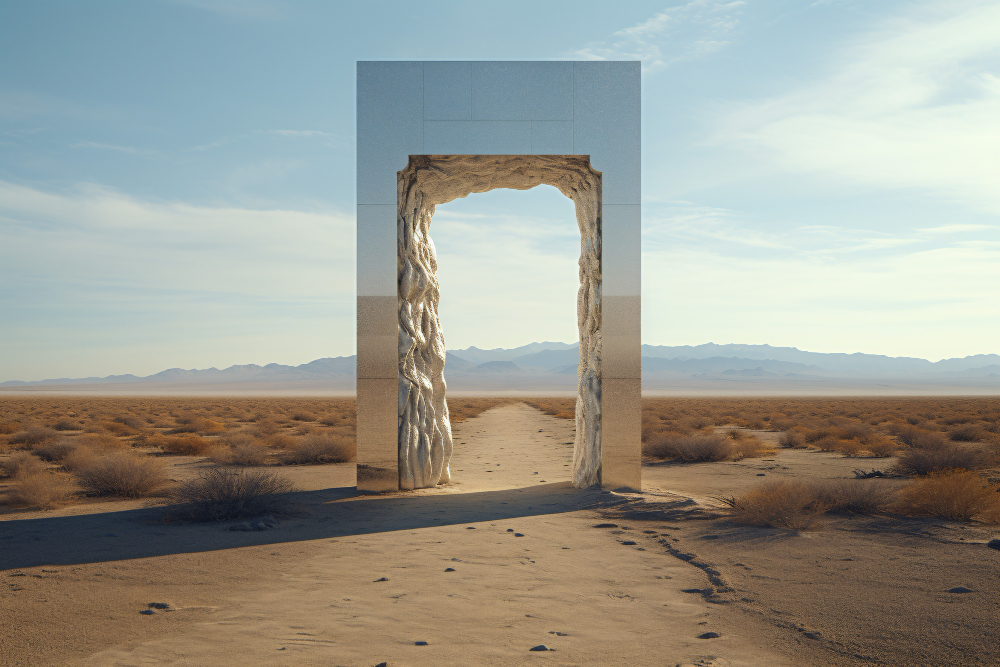
Of our industry experts, Webster is the most focused on disrupting mainstream manufacturing, citing window and door frame 3D printing as potential Forust opportunities. While regular wood is prone to warping, she says producing things from wood pulp allows you to “control certain factors, making the process desirable” to many in the furniture industry.
Similarly, Heinsman says “there’s still a lot to discover in architecture,” with 3D printed doors, window frames, ceilings, and furniture all seen as fertile ground for its technology. Though she adds that developing “reincarnated architecture” capable of constantly being recycled and adapted to users’ changing needs, remains “the ultimate dream.”
Wherever you look, from Vase Mode to Forust-made lamps, 3D printing is continuing to make inroads in custom design .
But ultimately it’s UltiMaker that’s reaching the broadest audience. Cura ‘Vase Mode’ continues to be a powerful tool for bringing custom aesthetic prints into peoples’ lives. With her Cura team also behind file sharing site Thingiverse, Maas says she keeps a close eye on uploads, and with makers continuing to innovate she believes they’re still the driving force in this space.
“If you look at Thingiverse, the things that get a lot of likes solve a problem that all 3D printing people have,” concluded Maas. “Things like knife holders, stuff that makes a 3D printer better, things that hold drill bits, even gifts for girlfriends or children.”
“We now support close to 600 printers, but these settings are also added by users. They find the settings that work for them, then share their work,” she added. “It’s not only our small team, it’s a big community of people. We’re just happy to be a part of the process.”