Soldiers setting up a SPEE3D machine to 3D print in the field. Image courtesy of SPEE3D.
The idea of establishing a digital part inventory that can be made physical on-demand continues to capture the imagination of manufacturers across industries.
With an innate ability to rapidly create highly complex components in low volumes, 3D printing has long been an attractive tool for bringing this idea into reality. From service providers such as Replique to larger engineering firms with 3D printing divisions like Würth, the industry is full of companies offering to help customers establish digital inventories of their own.
This should come as no surprise, digitized manufacturing brings numerous benefits: less material waste, minimal warehousing costs, and improved productivity – to name a few.
But the concept of virtual inventory isn’t just popular with those in industry, it’s gaining influence among defense leaders as well. Picture a unit of soldiers pinned down in their position, unable to progress due to a broken down vehicle or faulty equipment. With no time to wait for reinforcements, their very survival could depend on making spares on-site.
One of those seeking to offer a solution in this scenario that brings together digital inventory, 3D printing, and defense is 3D printer manufacturer SPEE3D. At this year’s Formnext trade show, I sat down with its CEO Byron Kennedy to talk through its efforts to bring shipping container-sized 3D printers into Western military supply chains, for spare part production on-demand.
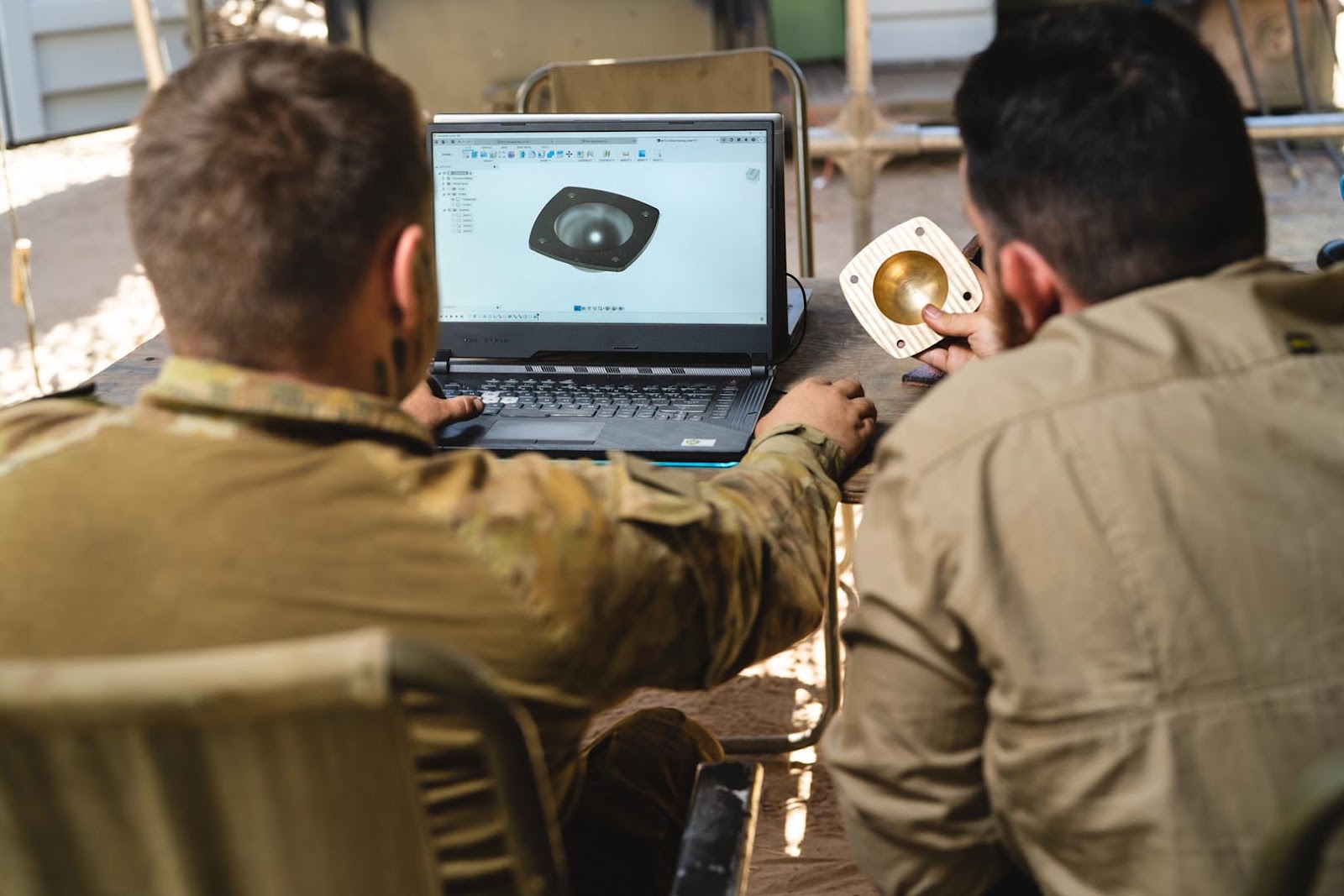
A CAD model of an end-use part designed for military vehicles. Image courtesy of SPEE3D.
Manufacturing at point of need
SPEE3D has established itself as an early leader in the emerging military 3D printing space. It has managed to achieve this thanks to its proprietary cold spray technology, which effectively sees metal particles sprayed onto a substrate at supersonic speed. Materials are jetted at such high velocity, the sheer force of kinetic energy binds them together into layered parts.
While SPEE3D doesn’t explicitly market this technology as a defense solution, its machines are all rugged, easy-to-transport printers, ideal for rapid deployment in tough terrain. This has made them an attractive on-demand manufacturing solution for many major militaries, including those of the US, UK, Australia, and even Ukraine – where they’re now used to make critical parts.
Kennedy sees the technology’s reliance on digitized designs as a massive advantage. “If you have a part that constantly breaks in the field, you can now redesign and make it stronger,” he says, adding that “it’s not just about lightweighting or material reduction.” In his view, design for additive manufacturing (DfAM) is a vital tool for rectifying flaws in unreliable parts.
He also sees the high usability of SPEE3D machines relative to traditional technologies as a potential gamechanger for troops in the field. “Let’s say you’re on the frontline, in a base in the middle of the desert or the sea. You really want to be able to pull out a file, hit print, maybe send a file for machining. It’s about making things as easy as possible.”
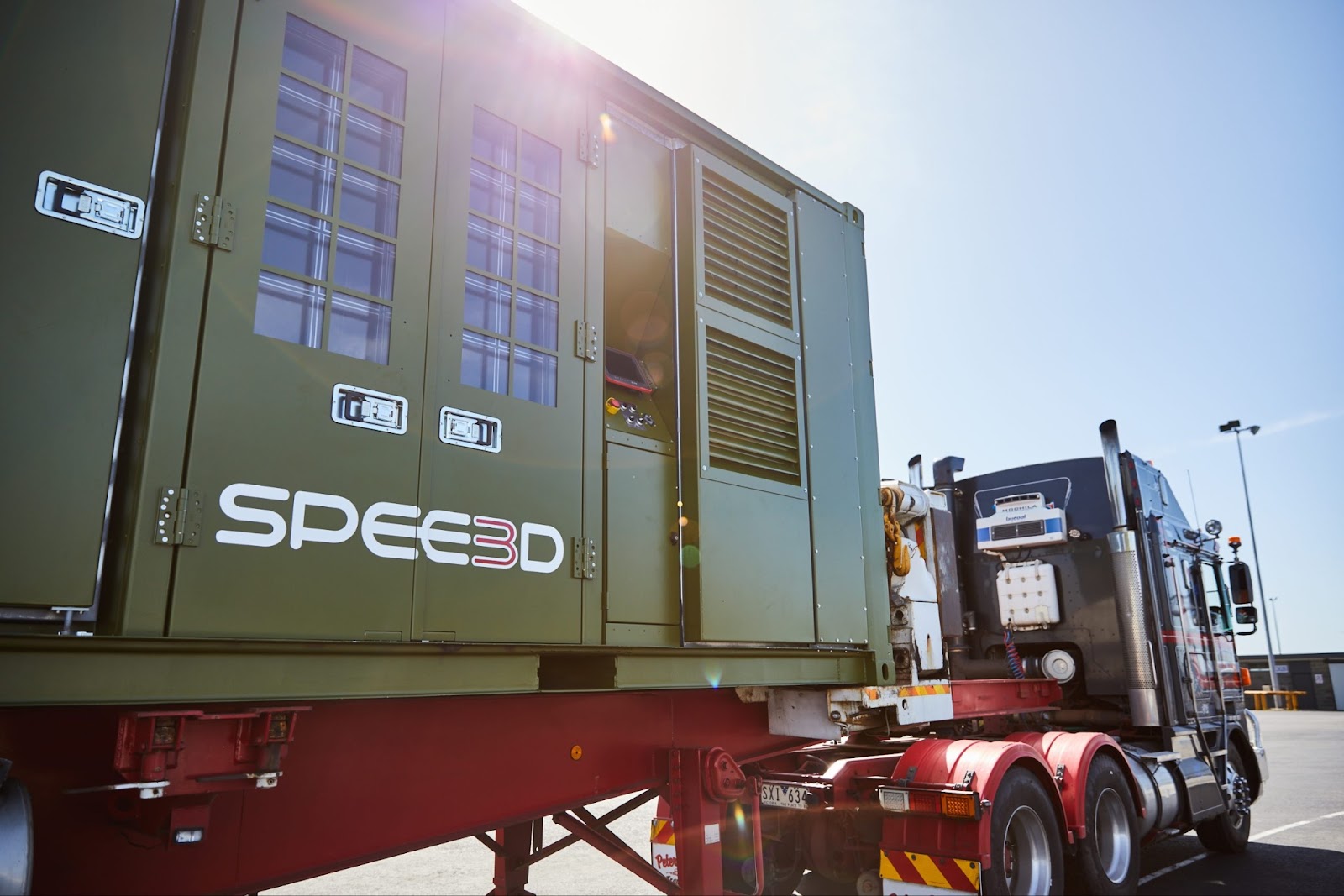
SPEE3D’s expeditionary manufacturing unit is designed for rapid deployment in the most hostile environments. Image courtesy of SPEE3D.
Tackling mission-critical challenges
While his company’s 3D printers create robust end-use parts, Kennedy admits that there are limits to their applications, saying “you’re not going to put these on an F-35 [fighter].” With there being such a high threshold for aerospace certification, he says it simply isn’t practical to try to gain full control over environmental factors, as would be necessary for printing in the field.
Instead, SPEE3D is focused on the mission-critical (parts essential to the completion of a mission), and the precision-critical (components with ultra-fine tolerances like nuclear submarine valves). Kennedy’s firm has already established a digital inventory of everything from Land Rover cylinders to alternator brackets, which can now be manufactured as required.
Moving forwards, Kennedy is confident that 3D printing can be integrated further into defense supply chains. Though he acknowledges that militaries already have complex spare part qualification workflows, he says it’s “simply a case of adapting to internal processes,” and applying good old-fashioned engineering to overcome any challenges that arise.
“People presume that with 3D printing at a high level, you push a button and a part comes out. No, there is engineering involved at every stage,” explained Kennedy. “You need to understand what parts are doing, level of risk, tolerancing, material properties. So you still have to engineer every single part. There are no shortcuts here.”
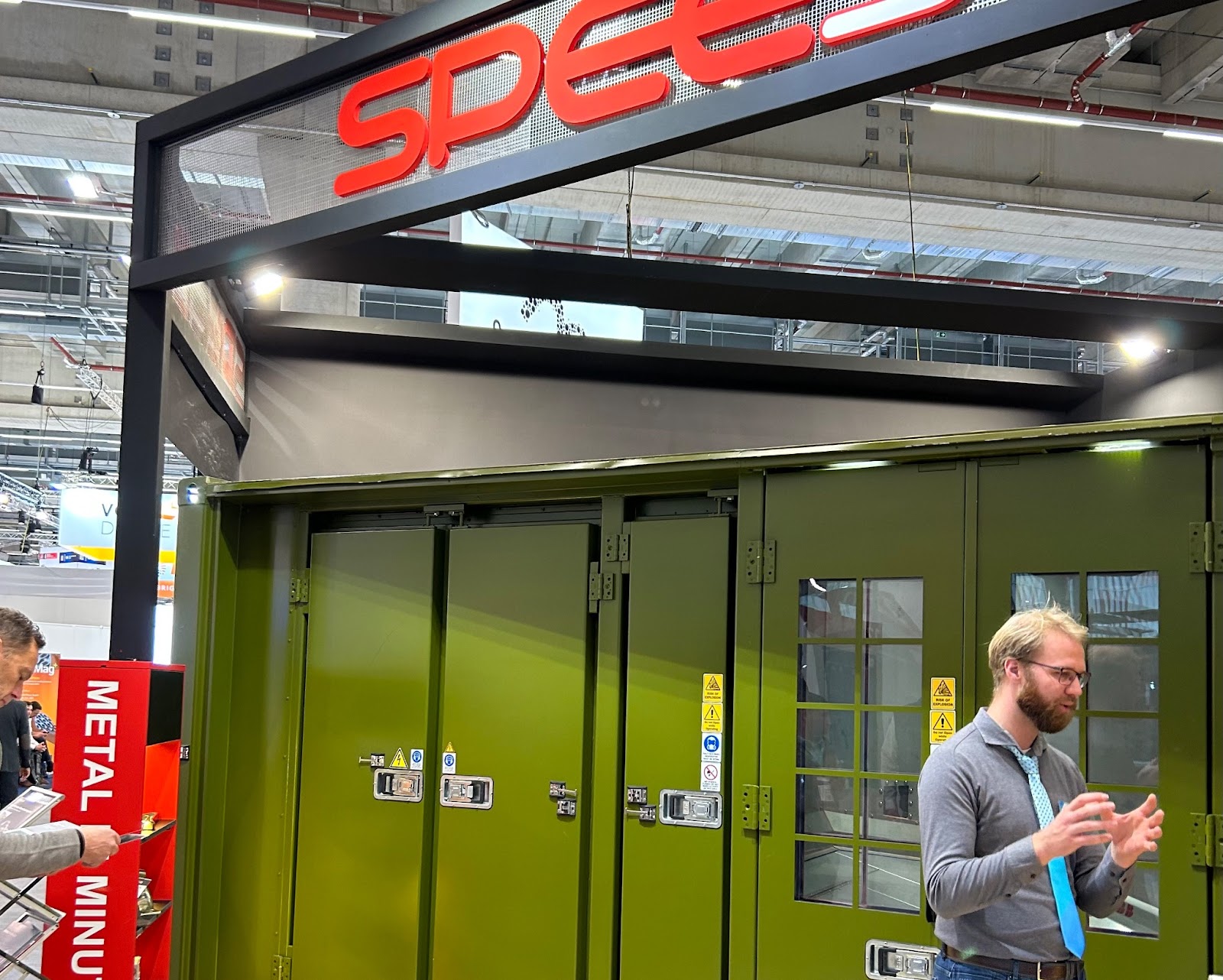
SPEE3D’s expeditionary manufacturing unit on-display at its Formnext 2024 booth. Photo by 3D Mag.
Taking things to the tactical edge
With our interview winding down, I wander over to the SPEE3D expeditionary manufacturing unit sitting opposite us. This colossal containerized system is capable of creating 0.9 x 0.7m parts weighing up to 40 kilos. And this isn’t theoretical either, the technology is already on deployment. No fewer than 13 SPEE3D machines are currently active in Ukraine.
At the company’s booth, Kennedy tells me about a recent US Navy exercise in which it was tasked with designing, 3D printing, treating, and machining a ship valve in under 4 hours. SPEE3D achieved this in just 3 hours 45 minutes – a huge saving on existing lead times of 2 weeks to 6 months.
Alongside field tests in both the US and the Australian outback, these results demonstrate the ongoing potential of on-demand 3D printing in the military sphere. With defense R&D budgets also going through the roof at the minute, SPEE3D seems well-placed to take advantage of this growing demand. It will be fascinating to see it ends up deploying 3D printing next.
One potential area of opportunity lies in manufacturing on the ‘tactical edge’ (with units close to combat). According to a DefenseNews report, the US Army is inching towards this objective. But Kennedy is keeping his company’s options open, concluding that they continue to target highly durable parts for land and sea, ready for use “under almost any conditions.”
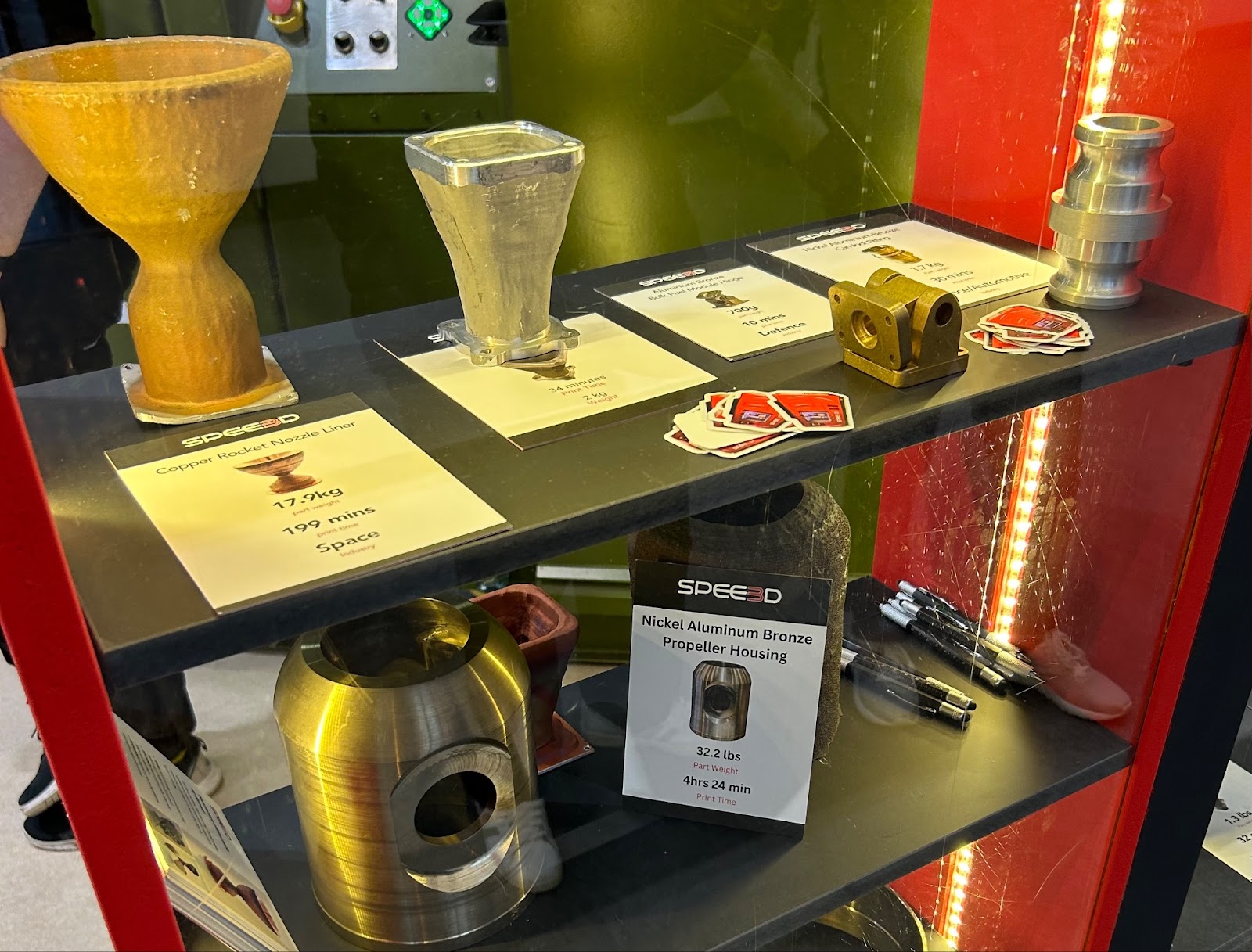
Cold spray 3D printed parts on-display at SPEE3D’s Formnext 2024 booth. Photo by 3D Mag.