Two years ago, Nikon announced plans to acquire SLM Solutions, a rising star on the metal 3D printing scene. This sent shockwaves across the industry – another huge multinational had followed the likes of GE and HP in throwing its weight behind additive manufacturing.
Of course, Nikon had already dipped its toe into the water, acquiring aerospace 3D printing specialist Morf3D in 2021. But taking over SLM Solutions – a fast-growing firm with customers like NASA, Boeing, and BMW – was a massive coup for a relatively new player in the field.
This acquisition was paired with further investments, in the shape of shares in software developer Ai Build, and Hybrid Manufacturing Technologies, a maker of systems with both additive and subtractive manufacturing capabilities.
Since then, Nikon has opted to manage its acquisitions under its Advanced Manufacturing division, ditching the Morf3D moniker for ‘Nikon AM Synergy,’ while adding its name to that of SLM Solutions. But what does the optics and photography giant plan to achieve in 3D printing? Does it intend to scale its ambitions further? How much vertical integration is going on?
To answer all these questions and more, 3D Mag sat down with Nikon Advanced Manufacturing CEO Hamid Zarringhalam at Formnext 2024, to discuss Nikon’s wider 3D printing ambitions.
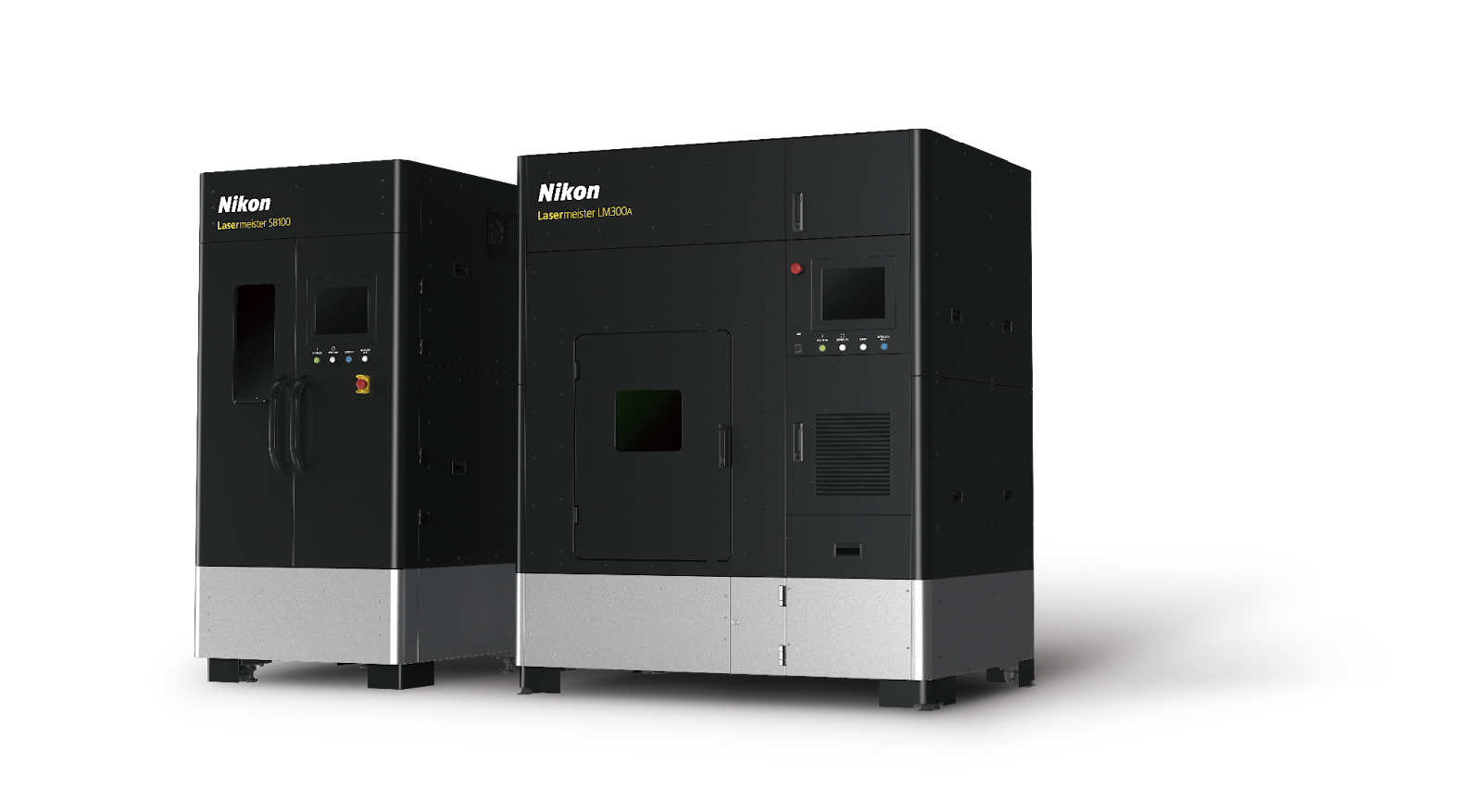
Nikon’s latest in-house-developed Lasermeister SB100 3D scanner & LM300A 3D printer. Image courtesy of Nikon.
Entering 3D printing at full throttle
Though Nikon is best known for high-end camera equipment, its business spans the wider optics, industrial metrology, and healthcare industries. Built up over 107 years, the company’s broad portfolio reflects its willingness to adapt and grasp fresh opportunities as they arise.
It’s in this spirit that Nikon began looking for ways to meet digitization demand during the early 2010s. Zarringhalam says digital design – the idea of going from virtual model to end-product – was seen as “the next stage for manufacturing.” With the fast-growing, lucrative automotive and aerospace sectors also becoming appealing, he explained that this led to an “investment into understanding the 3D printing market.”
Nikon followed this up with the acquisition of Morf3D and the launch of its own directed energy deposition (DED) 3D printer: the Lasermeister 100A. However, internal research soon found that laser powder bed fusion (LPBF) was the most pervasive form of 3D printing in manufacturing at the time – so Zarringhalam says it was only natural to pursue opportunities in this market too.
“That led us to connect with SLM Solutions,” explained Zarringhalam. “We saw that there was a lot of good chemistry and synergy. We felt that we could contribute to their evolution and solve some of the industry’s technology issues, with our pedigree in addition to our scale.”
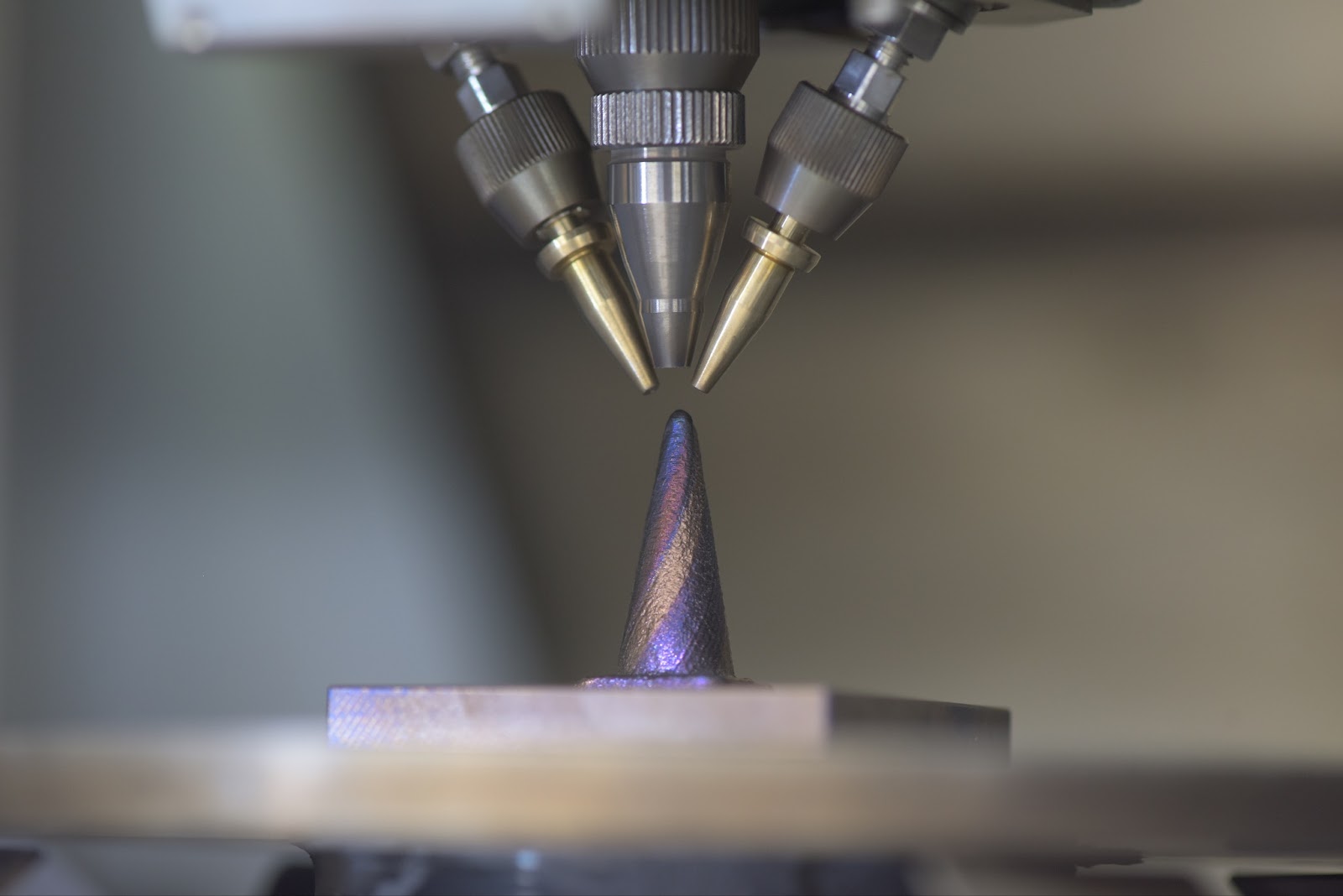
A cone-shaped object being 3D printed with a Lasermeister system. Image courtesy of Nikon.
What next for Nikon SLM Solutions?
While Morf3D has been renamed Nikon AM Synergy, relocated to California, and realigned to aid the wider adoption of Nikon’s 3D printing solutions, SLM has largely retained its branding and ethos. Now ‘Nikon SLM Solutions,’ the company operates independently under the Nikon Advanced Manufacturing division, marketing the same innovative technologies as before.
This includes the NXG XII 600, a massive 12-laser machine with a 600 x 600 x 600 mm build volume, which had become a key driver of SLM Solutions’ commercial success prior to its takeover. Already operational in defense, aerospace, and automotive, the system has provided Nikon with an ideal means of tapping into many of its key target markets.
One of the more eye-catching applications of this technology has been developed by Czinger Vehicles and Divergent Technologies. Divergent has established a vehicle production workflow that harnesses generative design and 3D printing to make and assemble custom parts on the fly. Not just ultra-efficient, this approach has yielded incredible new designs like the Czinger 21C – a 219 mph hypercar with 3D printed chassis, suspension, and engine components.
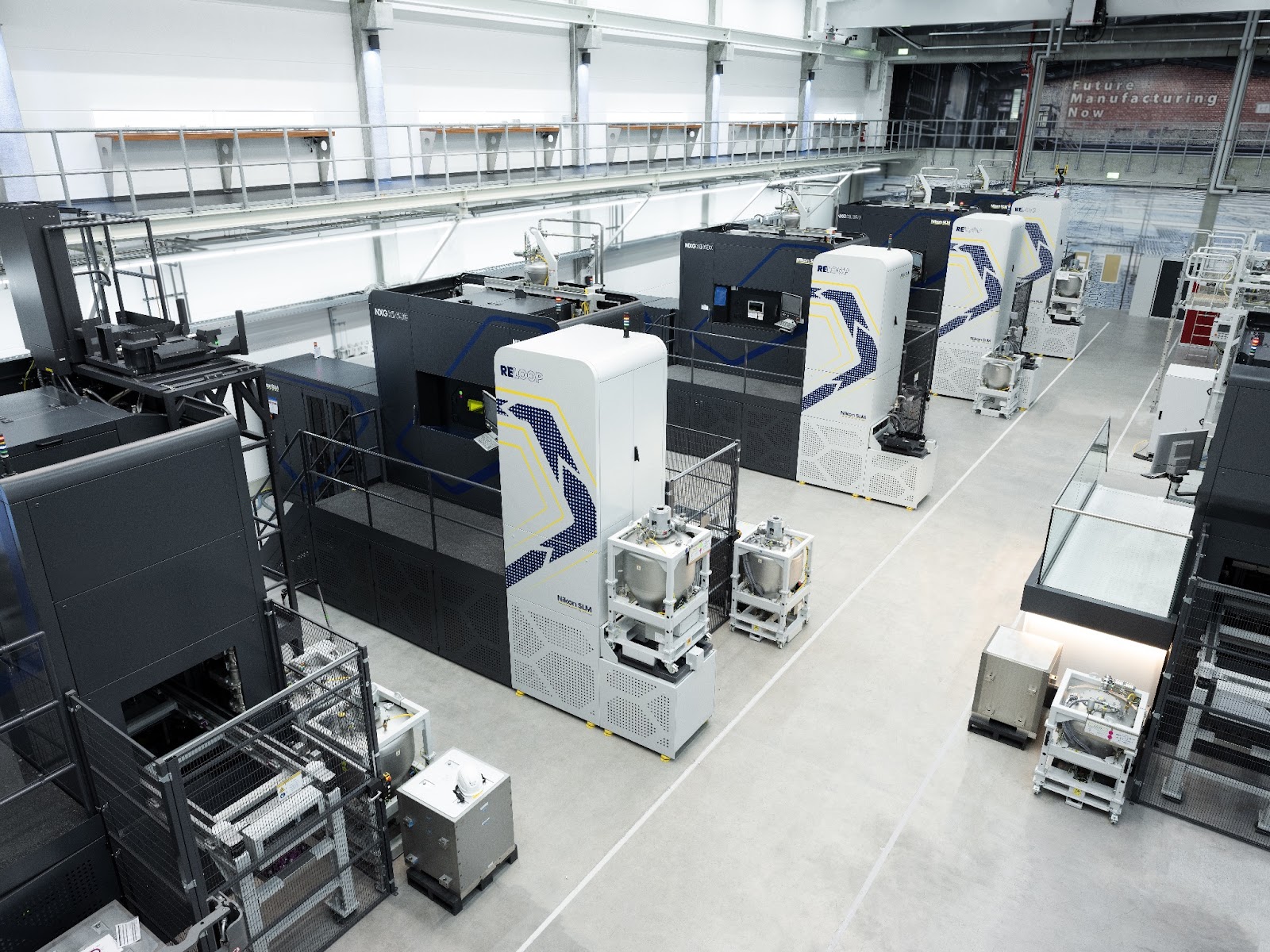
A row of NXG XII 600 3D printers. Image courtesy of Nikon.
Asked why he thinks NXG XII 600 3D printing has become so popular, Zarringhalam highlighted how it unlocks “freedom of design and the ability to make complex parts that are impossible monolithically.” He added that not having to stitch parts together allows for higher performance and lightweighting, while providing users with cost and lead time returns.
Moving forwards, Zarringhalam says there is scope for deploying the technology internally, but emphasized that this will “probably never be on the same scale” as fellow heavyweight 3D printing entrants GE. Instead, Nikon foresees making inroads in areas like energy, defense, and aerospace. Ideal for complex manufacturing at pace, SLM Solutions 3D printing is expected to continue finding applications in the production of UAVs, munitions, and more.
Targeting further growth
Nikon has huge ambitions – Zarringhalam says “the aspiration is to turn 3D printing into a billion-dollar business.” With the company having already achieved this in the flat panel and semiconductor industries, you could argue that his confidence is well-placed.
But in order to realize that potential, he adds that “close customer collaboration, shared roadmaps, and standardization” are all needed. Only then, he argues, can designs be tuned and materials be rapidly qualified so that users truly get the most out of the technology.
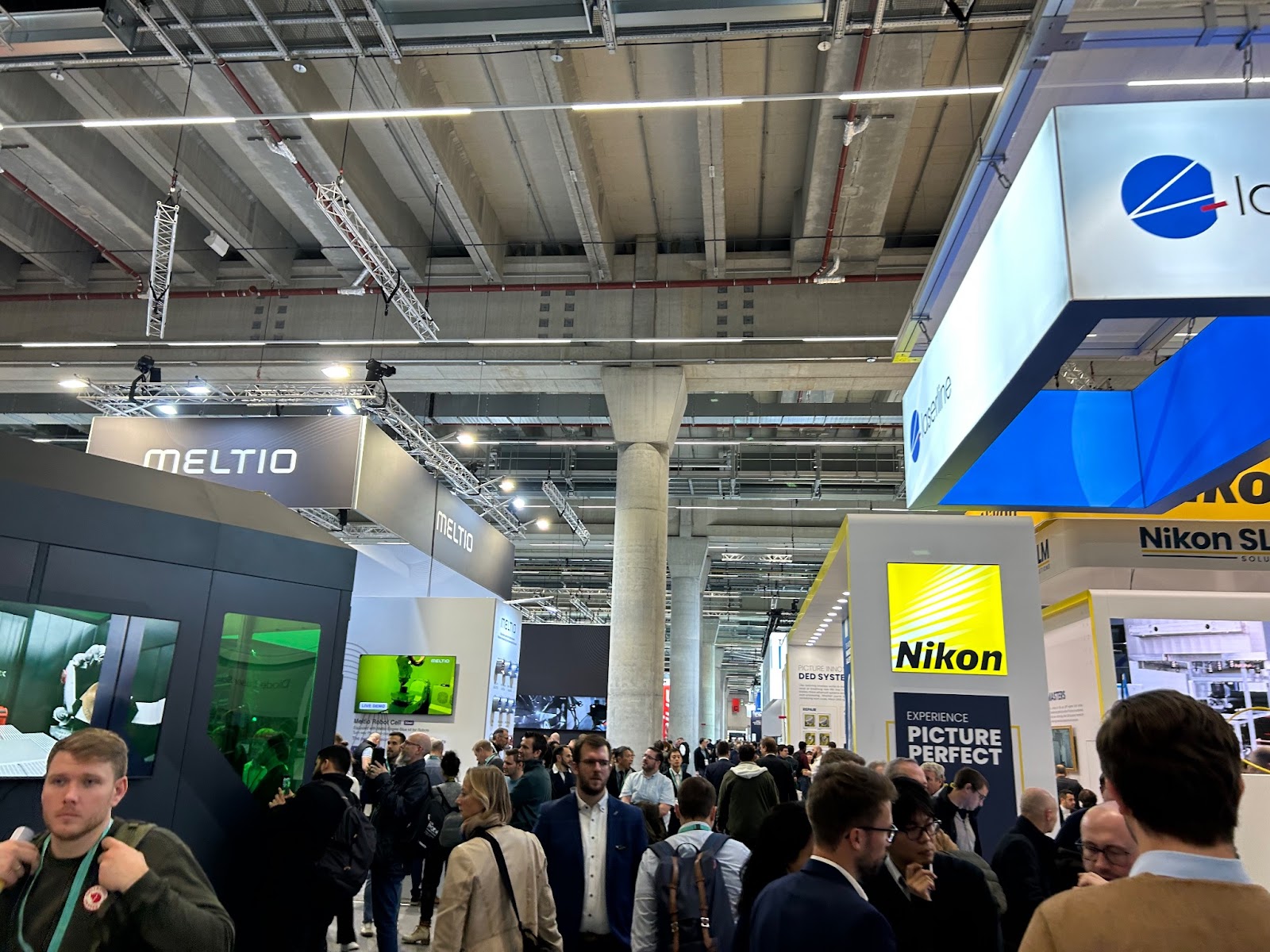
Nikon’s booth at Formnext 2024. Image by 3D Mag.
“This is no secret – the solution that offers the right product, at the right time, at the right cost, is going to win,” said Zarringhalam. “We’ve made tremendous improvements in driving down cost, our organization is obsessed with our customers’ journeys toward productivity, and we’re committed to eliminating variability. Almost all of this can happen by investing in R&D and customer collaboration.”
Following our interview, I toured the company’s Formnext booth and there was plenty to validate Zarringhalam’s claims about Nikon 3D printing’s potential. From Saab underwater vehicle tail sections to Emerson pipeline valves, the broad appeal of the technology was clear to see.
With Nikon SLM Solutions announcing the sale of its 1,000th machine to Bosch late last year, it’s equally obvious that for Nikon, the future is now. Where next for Nikon’s 3D printing efforts? It seems like the only way is up for Zarringhalam and his firm’s acquired team of experts.
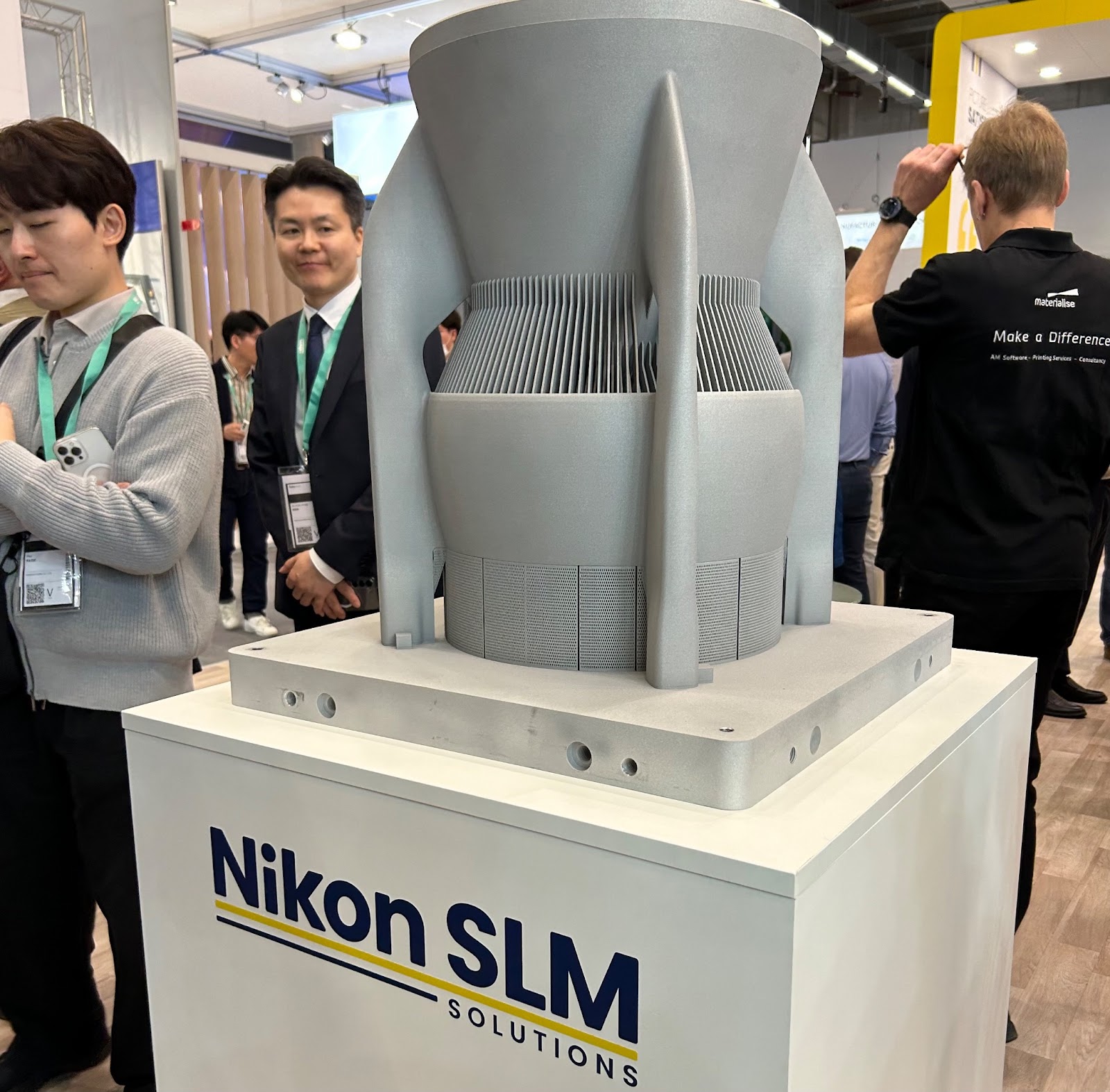
An impressively large 3D printed AUV tail section on-display at Nikon’s Formnext booth. Image by 3D Mag.