The world of extrusion 3D printing can be a confusing one for newcomers. This is particularly the case with materials, an area in which 3D printer manufacturers must seem to throw acronyms around like confetti. Whether it be ‘TPU,’ ‘HIPS,’ or ‘PVA,’ the language is likely to baffle if you’re not fully familiar with the technology, or just getting to know it.
With the material palette of modern 3D printers continuing to grow broader by the year, it’s difficult to stay up-to-date with every blend that makes it to market, but there are two that are definitely worth getting to know: ABS and PLA. Compatible with pretty much all hobbyist machines, these materials are stalwarts of the desktop 3D printing scene.
But when it comes to PLA vs ABS 3D printing, which is best? Let’s take a look at what each of the popular polymers is made of, where they’re best utilized, and how they stack up against each other.
Read our overview about all common 3D printing materials.
What are ABS and PLA?
To begin with, it’s worth breaking down the compositions of both materials.
Polylactic acid or ‘PLA’ is a thermoplastic polyester made up of natural ingredients like corn, maize, or sugar cane. As a result, it’s often described as bio-sourced and biodegradable. Given that it’s the most-used material in 3D printing, that’s a good thing, right?
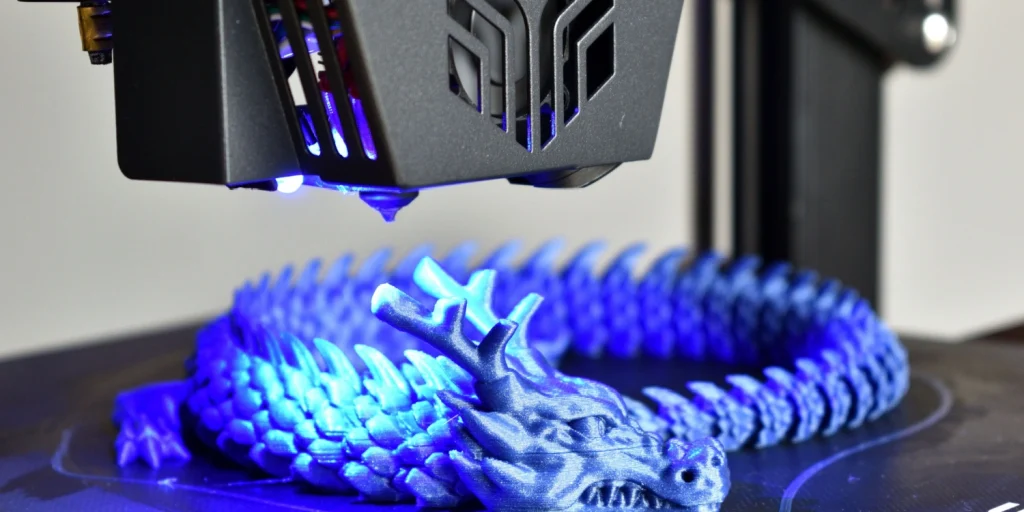
In terms of how the filament’s constituent parts are sourced – absolutely. However, the term biodegradable doesn’t necessarily mean compostable, and used PLA is often thrown away rather than recycled, or processed into eco-friendly compost. In practice, it’s also easy to print, and stiffer than ABS materials like nylon, but it doesn’t respond well to high temperatures.
Acrylonitrile butadiene styrene or ‘ABS,’ on the other hand, is not biodegradable, but it can be recycled multiple times. Composed of acrylonitrile, butadiene, and styrene, the typically opaque polymer tends to be tough, lightweight, and durable. Where ABS stumbles is in its usability: it can require higher print temperatures, creates odors, and – though it’s better than PLA at deflecting heat – it’s hardly an industry leader in that area, either.
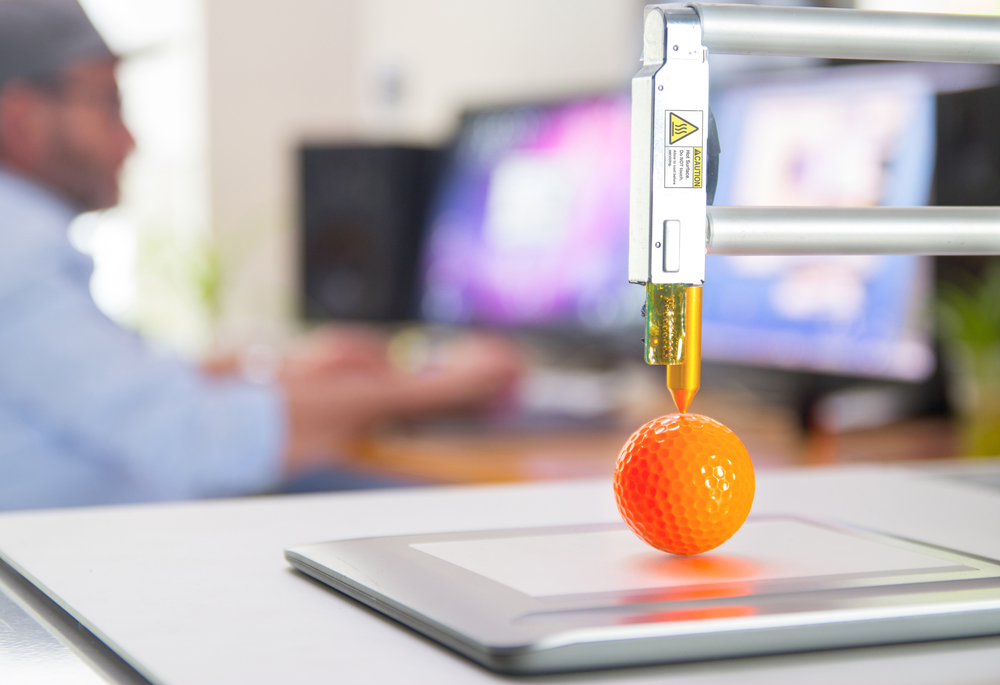
ABS vs PLA: strength
So, that’s what they’re made of, but what are the properties of ABS and PLA?
Let’s start with an important one: strength. On this count, parts 3D printed from both materials actually have very similar characteristics. However, those made with ABS are often less dense, more impact-resistant, and have a higher elongation at break, meaning that they’re less vulnerable to breakage when their shape is distorted.
These features have long made ABS a better option for creating end-use components like car bumpers.
By contrast, PLA has a higher tensile strength – the maximum tensile stress it can take without breaking – while also being more brittle and less flexible. Their properties therefore lend themselves to different applications, but neither can withstand much exposure to UV rays or moisture, meaning that they’re not well-suited to producing outdoor parts.
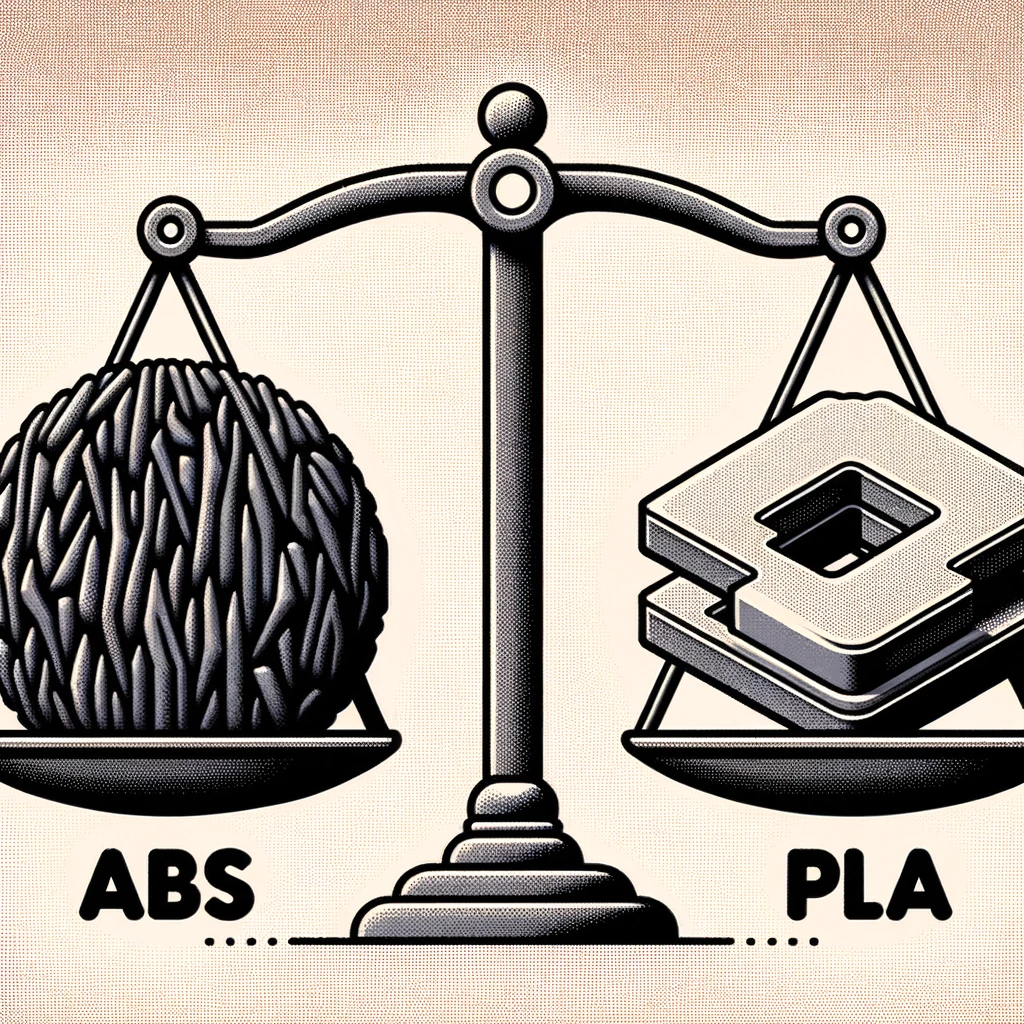
Those seeking to 3D print with the toughest possible plastic may even want to consider upgrading to PEEK. Sold by many well-known material resellers, including 3DGence and iMakr, it’s colorless and harder to process but it’s also lightweight and ultra-durable.
ABS vs PLA: melt temperature
When it comes to heat resistance, there is a much greater difference between the two materials. ABS features a glass transition temperature – the point at which a polymer goes from a hard to soft state – of 105oC, 45oC higher than that of PLA. This inherent limitation makes the latter more of a hobbyist material than one suited to creating end parts.
If, for example, you were to 3D print the top of a gear lever and the fitted part were to be exposed to direct sunlight, it would be more likely to melt if it were made from PLA.
That said, ABS’ higher heat resistance does come with drawbacks. The material is more difficult to print with, as such loftier temperatures make it prone to warping. To counteract this, ABS users can invest in a machine with a heated bed and more thermally resistant extruder, although this often drives up production costs. As a result, it could be said that adopting ABS is less worth the hassle for those modeling on their desktop.
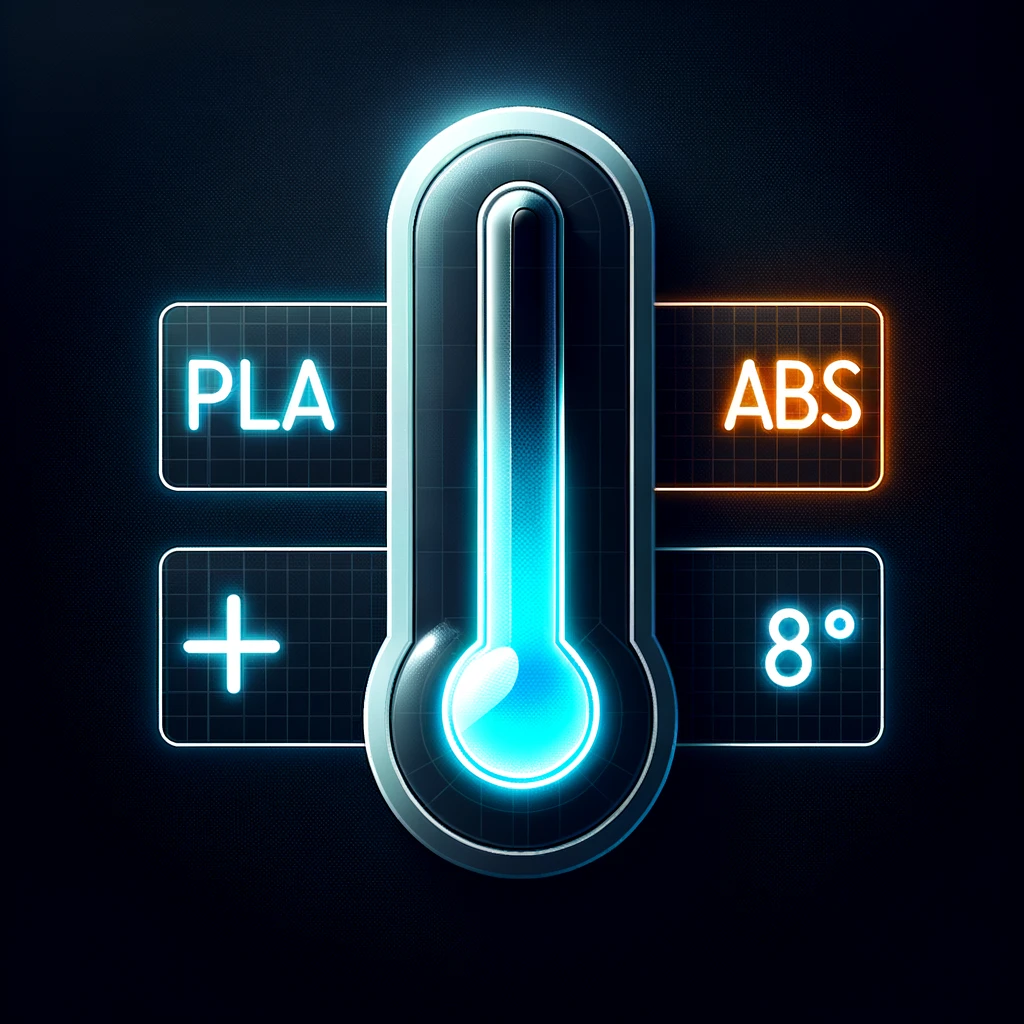
ABS vs PLA: surface quality
Of course, no matter which material you use, fused deposition modeling (FDM)-printed components are always going to have layer lines, but those made with ABS and PLA often have visible differences. While the former tend to feature a matte finish, the latter are often more glossy. While it’s possible to post-process parts made from either, makers seeking to create models with high levels of detail, should probably consider resin 3D printing.
Another aspect of 3D printing that’s worth considering when it comes to surface quality is accuracy. With both materials it’s possible to create parts with fine details, although users will need to factor in tolerances for connecting and interlocking parts, to ensure they fit.
If anything, PLA has a slight advantage in this area due to its lower print temperature. This is because it’s less likely to warp, and easier to print sharp corners and fine features with. That being said, part accuracy naturally has more to do with 3D printer specification and setup than it does with feedstock, so if accuracy is your number one priority, machine choice is key.
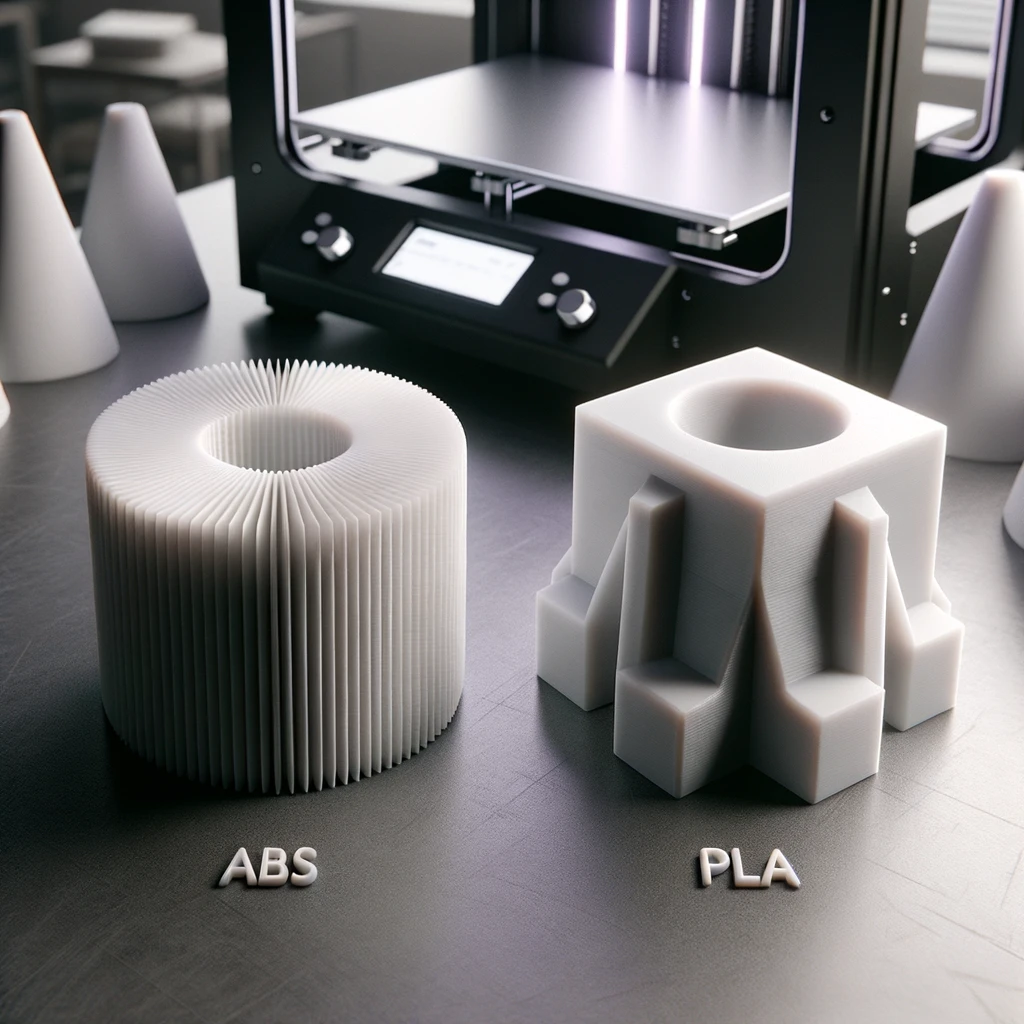
ABS vs PLA: print speed
The good news for desktop 3D printer users is that PLA and ABS can be printed at pretty much the same speed. When switching materials, that means you don’t need to change slicer settings, saving you the time and hassle of having to do so.
They do have different speed limits though. While PLA is generally extruded at speeds of 60mm per second (mm/s), it can be printed at much higher speeds of over 150 mm/s. ABS, meanwhile, tends to have a working range of 40-60 mm/s, a window that can be a limitation for high-throughput users.
ABS vs PLA: accessibility
Lastly, it’s also worth considering how easy it is to start using ABS and PLA respectively. After all, if you’re completely new to desktop 3D printing, the last thing you need is a complex setup that requires excessive tinkering. As mentioned above, the heat resistance of ABS makes it more difficult to print, but the results of this thermal stability do speak for themselves.
As it’s often used for injection molding, a far more widely-used technology, ABS is generally also a little cheaper. On the flipside, however, PLA is arguably better to print with, as it yields stronger, stiffer parts, and its ubiquity means there are more variants and colors available – ColorFabb, for example, now offers the material in over 200 shades.
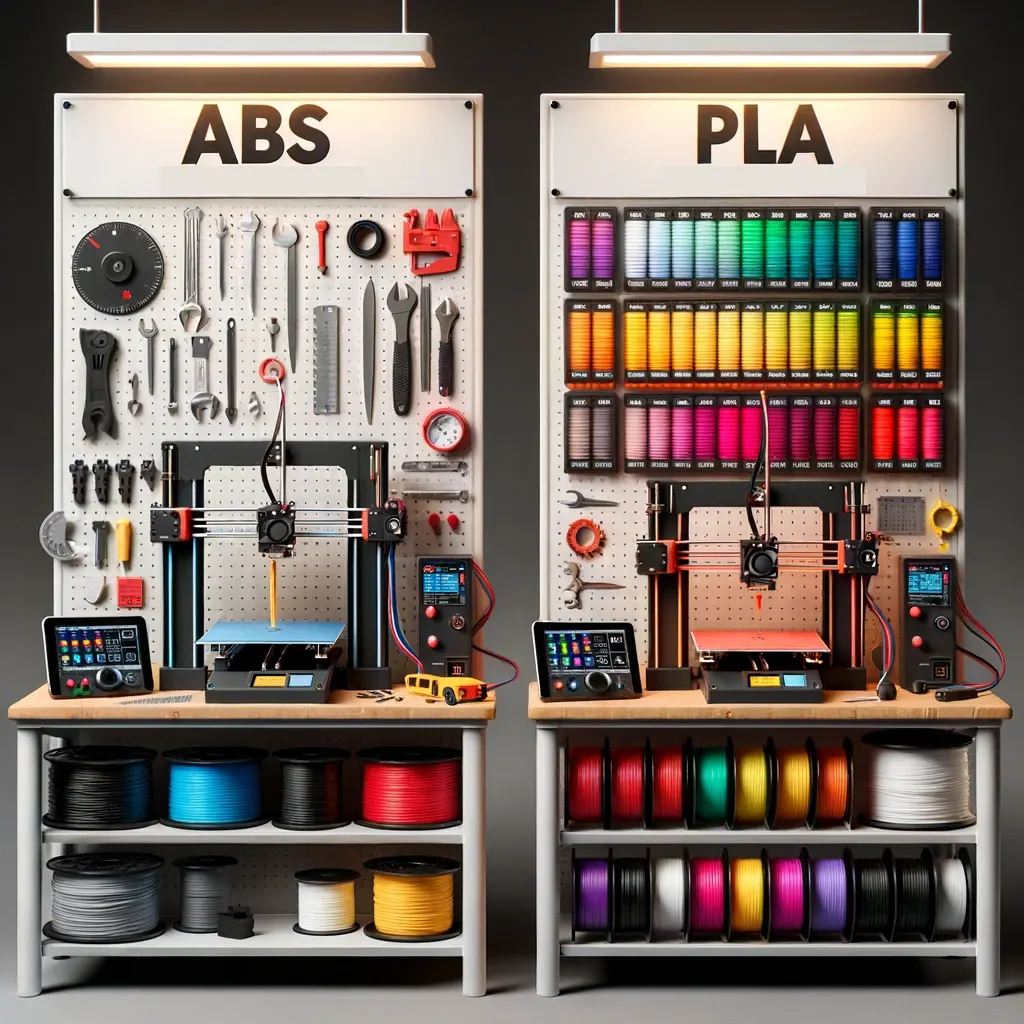
PLA vs ABS filament: when to use each
As you can tell from our above comparison, there is no clear winner between ABS and PLA. They’re available at a similar price point and the variety seen in the ABS market is now catching up to that of PLA’s. Where they differ is in print temperature, with ABS requiring users to run a machine with a heated bed, and (ideally) an enclosed chamber.
To reiterate, ABS’ light weight, as well as its impact and thermal resistance properties, also lend it to more low-load end-use applications than PLA, which is better suited to prototyping.
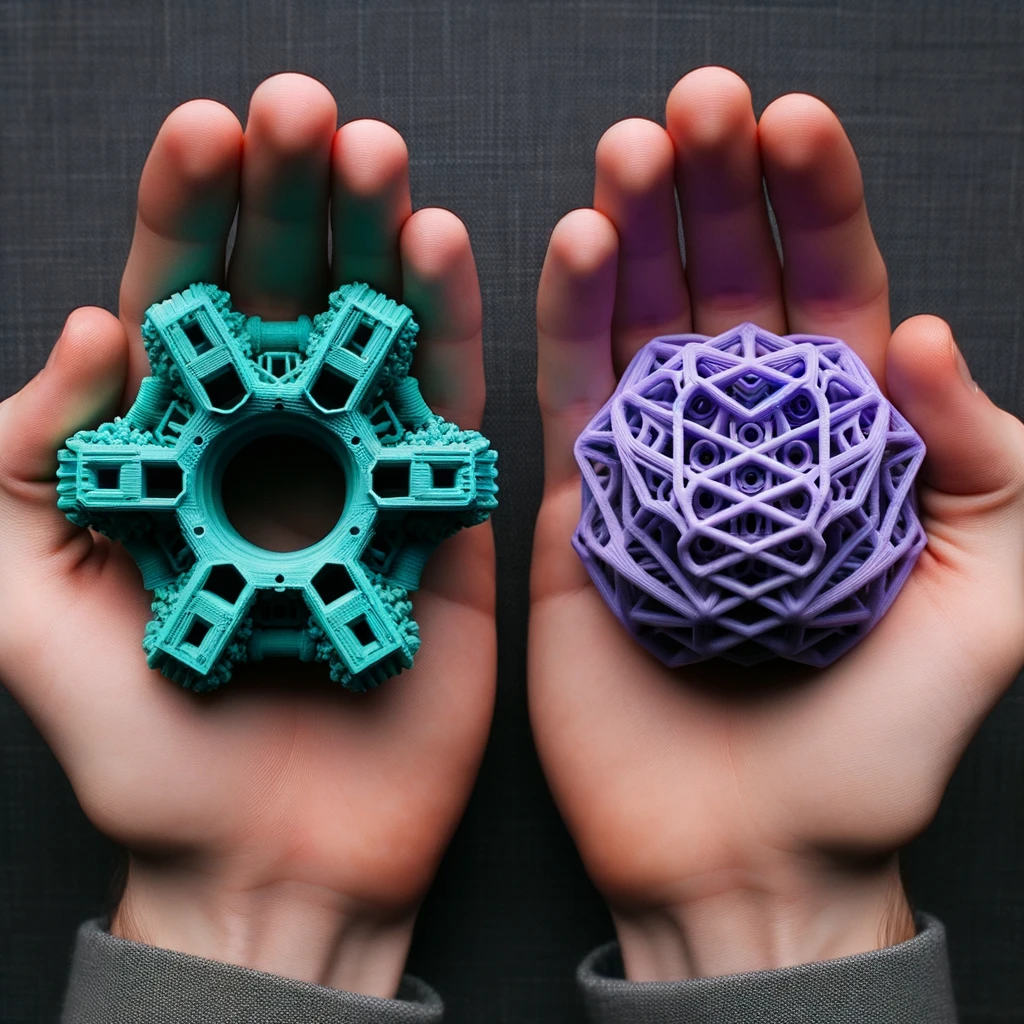
Though that’s not to say there’s nothing you can do to overcome the drawbacks of either material. With ABS, there are systems out there with print beds designed to improve adhesion and reduce warping, so there are ways around its vulnerability to heat deformity. When using PLA, on the other hand, you can tackle oozing by tweaking your unit’s retraction settings.
As a result, as is the case in so many debates around 3D printing, this one’s a matter of application. If you’re manufacturing parts for use in factory environments where temperatures are likely to fluctuate, you’re better off using ABS than risking printing them from PLA. But if you’re printing at home, in thermally stable areas, most models, even basic brackets, jigs, and fixtures, can be produced more easily with 3D printing’s most widely-used material.
Hi there!
Do you have a plans to make a big overview for whole existing 3d printing materials? Wood, glass or something like that? And if it possible with results of trying any of it