It’s an age-old debate in the world of 3D printing: which yields better parts, resin or filament?
Resin and filament 3D printing first came to be between 1988 and 1991, when 3D Systems and Stratasys launched their inaugural stereolithography (SLA) and fused deposition modeling (FDM) machines.
Read our overview on common 3D printing materials to find out more.
In terms of sheer popularity, these two system types stand head and shoulders above all the other 3D printing technologies that have launched since, but that’s not to say they’ve stood still. On the contrary, the SLA and FDM processes behind the firms’ foundational units continue to advance, in a way that still drives cross-industry innovation to this day.
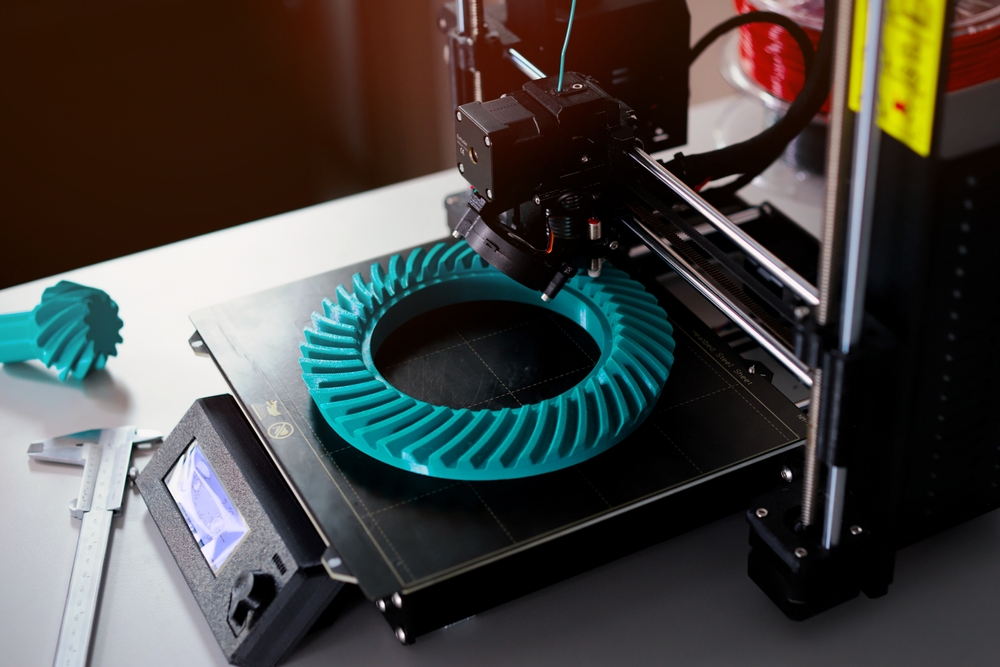
The same can be said for the breadth of the materials available for each technology. Gone are the days when you could only use plastics. Now, you can print with anything from metals and ceramics to human cells, but which of these feedstocks is best?
To try and answer that fundamental question (or at least see which is best at time of writing in 2023), it’s important to distinguish between material and machine benefits. Let’s start with a quick comparison of how the technologies stack up against each other.
Resin vs filament 3D printing
While there are many different types of resin 3D printing including SLA, masked SLA (MSLA), digital light processing (DLP), and more, they all involve the layer-by-layer curing of liquid resin into 3D objects. SLA, the most popular of these, is renowned for enabling the creation of parts with a smooth surface finish that don’t feature the layer lines seen in FDM prints.
This has made the technology particularly appealing to designers and model-makers seeking high-quality mock-ups and figurines. Some of SLA’s other benefits include the ability to create isotropic parts – those with properties that are the same when tested in multiple directions – as well as objects with a level of watertightness that’s well beyond filament-based prints.
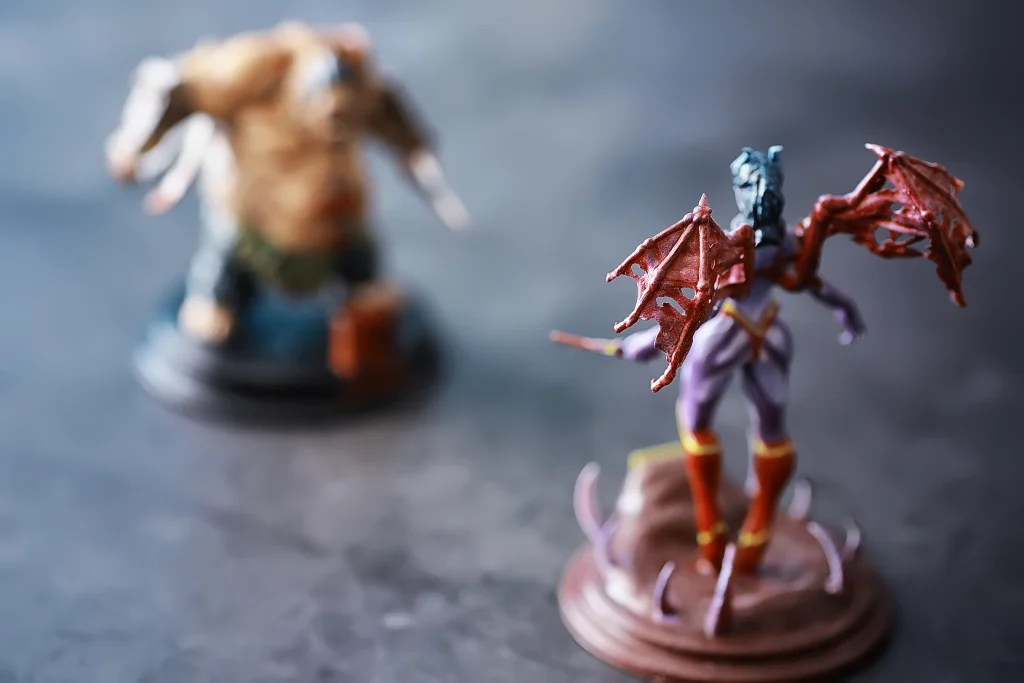
Extrusion 3D printers, meanwhile, tend to be considerably less sophisticated. Most desktop ‘bedslinger’ systems are composed of a build platform on which filament is deposited layer-by-layer by a heated nozzle. Switching FDM materials stored on cardboard or plastic reels is generally considerably easier than refilling resin 3D printers. This is because resins can be toxic and highly flammable, thus they need handling with safety equipment.
In addition to being lower maintenance, FDM 3D printing also allows users to create parts with varying levels of density. Through changing the level of a part’s infill, it’s possible to produce objects that are entirely hollow or almost completely dense on the same machine.
By printing infill in certain patterns, you can even create parts that dampen and amplify sound or heat in a way that’s simply impossible to do with entry-level resin systems.
When it comes to speed, you can accelerate your rate of FDM 3D printing by choosing to print with thicker layers, but this will inevitably impact the quality of your models. Additionally, this will almost certainly be slower than creating the same object with SLA, as the latter focuses energy more directly, and solidifies material faster.
As you can already see, there are many pros and cons to FDM and SLA 3D printing. Having gone through the core differences between the technologies, it’s now worth breaking down the pros and cons of working with resin and filament in more detail.
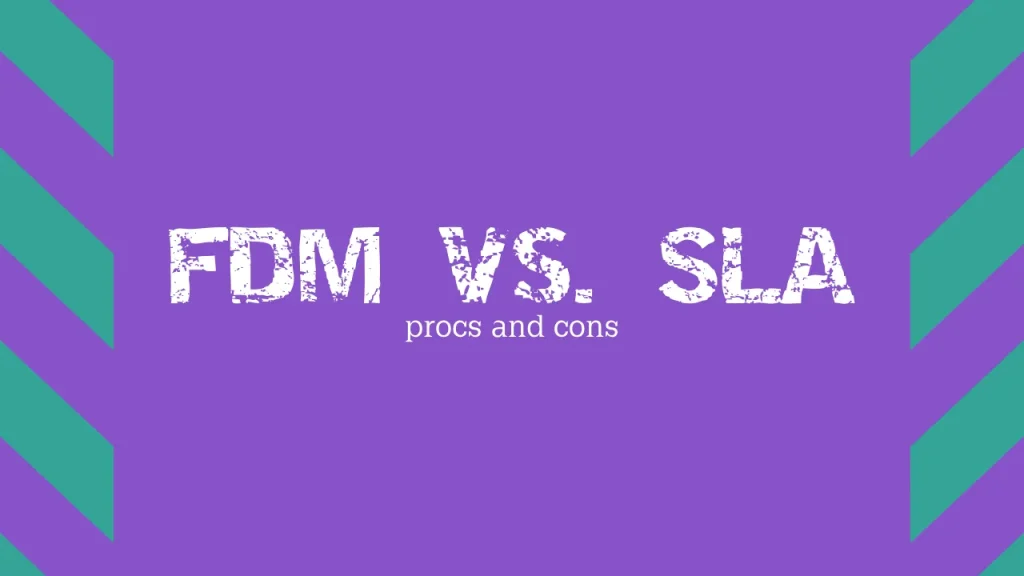
Pros: filament 3D printing
- Compared to SLA 3D printing, there’s a much greater variability in performance between FDM machines, but there are still several benefits that all filament users enjoy. As adopters of the most popular 3D printing technology out there, they have access to the widest range of materials. This now includes everything from flexible elastomers to certain metals.
- Thanks to this material diversity, extrusion has been able to grow well beyond its traditionally prototyping-focused base, into production environments. When strung together to create ‘print farms,’ for instance, extrusion machines can be used to reach high throughputs (at least by 3D printing standards) of end-use parts. Take Slant 3D, operator of the biggest print farm in the US. The firm now runs its printers 24/7 and churns out over 10,000 parts per week.
- Other benefits of FDM include affordability and accessibility. Although tasks like bed leveling are notorious for being difficult for newcomers, the technology is relatively easy to get to grips with. The general reliance of these machines on filament feedstock is central to this, as switching out materials is often as simple as changing one reel for another.
It can also be said that the most widely adopted filaments – thermoplastics – are far stronger than the photopolymers used in SLA. This is reflected in the durability of the parts you’re able to make with them.
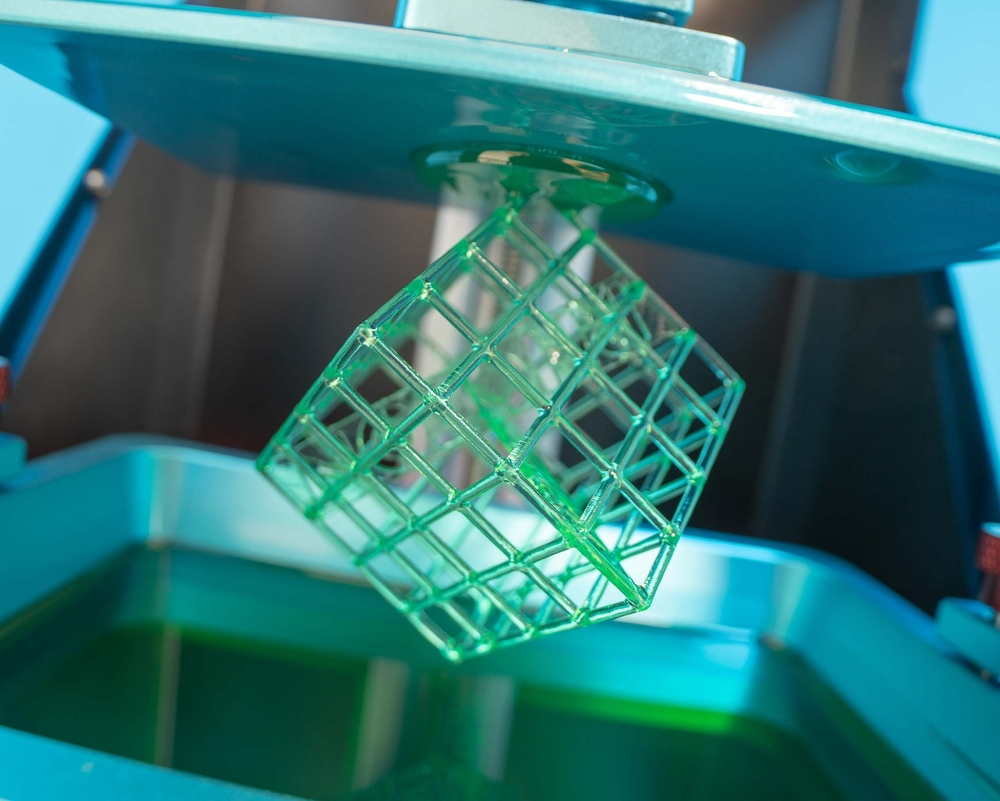
Stereolithography photopolymer
Cons: filament 3D printing
- One of the main drawbacks to filament 3D printing is the way it yields parts with visible layer lines. While it is possible to give FDM-printed objects a smooth surface finish, this requires post-processing, an additional step that increases both part costs and lead times.
- Another disadvantage to extrusion 3D printing is the anisotropic nature of the parts it produces. Caused by weak interlayer bonding, this can result in structures that fall apart under pressure. FDM prints must therefore be oriented correctly, especially when designed to be load-bearing. That said, ensuring this is the case requires a level of 3D software familiarity, but not to such an extent that it would be beyond most designers and engineers.
- Though not quite as high-maintenance as SLA, adopting FDM does also come with its own implications. Many entry-level extrusion machines are desktop-sized, so they can be installed virtually anywhere, right? Well, almost anywhere. Users still need to make space for things like filament storage, and the toxicity of the fumes emitted during production is still not fully understood. As a result, space and ventilation are still important aspects of FDM.
Pros: resin 3D printing
- Whether used with SLA, MSLA, or DLP 3D printers, resins yield parts with a higher quality surface finish than filaments do. This ability to produce models with fine details as small as 25 microns has made resin systems particularly popular among desktop miniature makers. But their high resolution 3D printing capabilities have also made them a popular means of creating dental models and jewelry pieces with uniquely complex patterning.
- When it comes to photopolymers themselves, the light-sensitive resins are available in fewer variants than their extrudable counterparts. For example, some FDM machines now use pelletized feedstock. But the resin market is still seeing diversification, with traditional PLAs and ABS’ being joined by more flexible elastomers and silicone-like polymers.
Cons: resin 3D printing
- For 3D printing newcomers, the most obvious drawback to adopting resins is the level of care that has to go into handling materials. Liquid resins are toxic, giving off harmful fumes when printed, and touching them directly is known to cause skin irritation. As a result, users need to wear protective equipment like goggles and nitrile gloves, as well as taking care to transport hazardous materials in the correct containers.
- All of these measures are considerably more stringent than those related to filament 3D printing, and it’s safe to say that most desktop users start with FDM before moving on to SLA.
- It’s also worth considering how resin 3D printed parts are made: UV light curing. This means there’s also a danger that heat or direct sunlight exposure could damage them. On average, SLA/MSLA/DLP 3D systems are more expensive than extrusion machines as well. That’s not to say there aren’t bargains out there – you can still get SLA units for a few hundred dollars – but it does make them a complicated, costlier option, especially for the inexperienced.
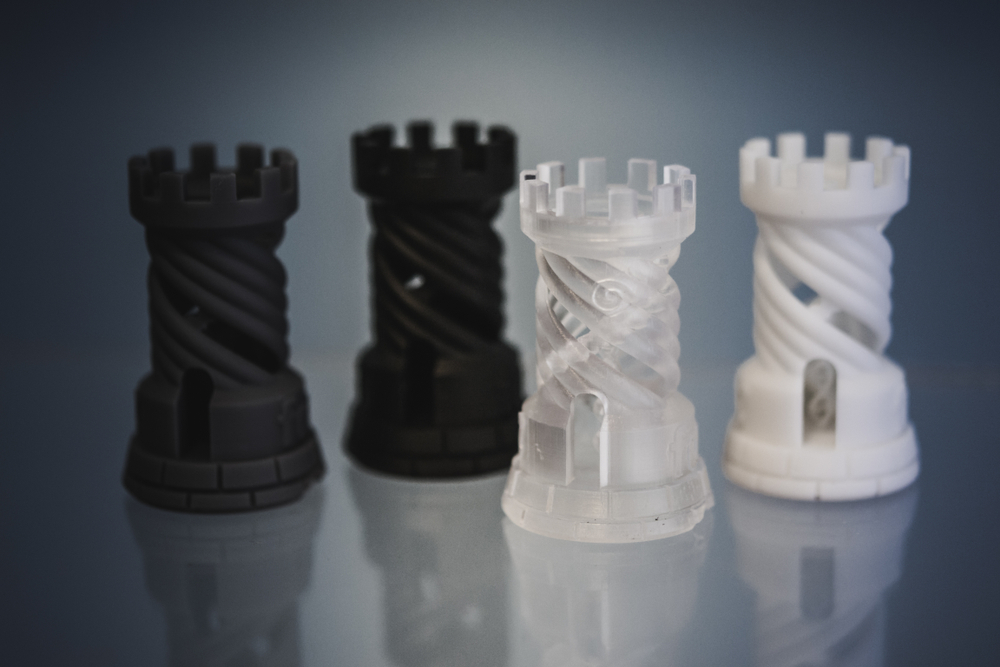
Resin vs filament: is there a winner?
As you can see, there are a lot of intricate differences between resin and filament 3D printing that make choosing a definitive winner between them difficult. These are complicated further by the variations between 3D printers themselves, as some are better at hiding the shortcomings of their base UV curing or extrusion technologies than others.
However, at a more fundamental level, there are also pros and cons that apply to virtually all resin and filament 3D printers. The former are great for creating detailed models with smooth surface finishes, while the latter tend to be more accessible, faster, and yield durable parts. In reality, this means that resins and filaments are suited to very different applications.
With the right feedstock, FDM can be used to create incredibly rugged components, and the technology continues to address applications in the demanding aviation and aerospace industries. On the flipside, SLA is better suited to the production of consumer and clinical products with finer surface finishes – think toys, electronics, or dental crowns.
What does all this mean for the great resin vs filament 3D printing debate? It means that right now at least, there isn’t a clear winner. It’s more a case of finding which technology, system, and material combination is best for your use case, and going from there!
Great breakdown of the pros and cons! I’ve been trying to decide between resin and filament printing for my projects. Your insights really helped clarify the differences. I’m leaning towards resin for detailed models but still appreciate the practicality of filament for larger prints. Thanks for sharing!