3D printing used to be all about polymers, but now you can use all sorts of materials: metals, woods, foams, if it’s used in manufacturing, it’s increasingly possible to print with it.
These materials also come in various formats ranging from resins and powders to filaments, so how can you find the best one for your machine? Largely, this will depend on your application and the design concept you’re hoping to realize. Also, this great new feature creates opportunities for a large variety of new jobs. You can find a lot of 3d printing related roles, such as 3d modelier at jooble.
If, for example, you want to create detailed desktop miniatures, you’ll need to make them from a material that yields prints with a sealed, high quality surface finish. On the flipside, if your aim is to create a part that’s designed for continued usage, it’ll have to be printed using something more robust, with high strength, durability, and maybe even weather resistance.
To help you get an idea of what technology and feedstock you might need, let’s take a look at some of the more popular choices – including a few versatile materials capable of ‘traveling’ from one type of printer to another.
SLA: Resins
For prototypes, miniatures, and models for end-use or proof of concept purposes – especially those featuring a high level of detail – 3D printing resin is your best choice. Solidified with UV light and usable with technologies such as stereolithography (SLA), masked SLA (MSLA), and digital light processing (DLP), resin is a chemically resistant photo-reactive material.
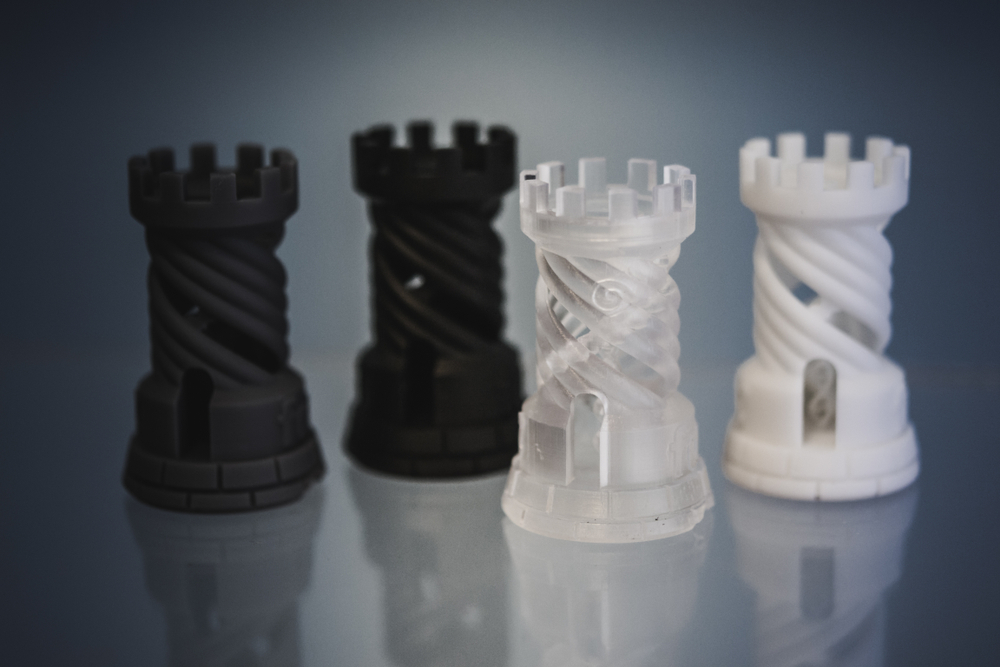
Resins are not just economical, they’re strong enough that resin 3D printed parts can be machined afterwards. With resin 3D printing, you can also create parts with layers as thin as 0.05 mm, much narrower than those of regular filament-fed machines. This means they can be used to create models with a higher quality, smoother surface finish.
These materials are now developed in a fair amount of varieties, including flexible, tough, washable, and even plant-based iterations.
What all these resins have in common, is that they can be used in 3D printers that are faster than extrusion systems. In terms of downsides, the technology is more costly to use, doesn’t feature composite printing compatibility and – it has to be said – it tends to be a bit stinky, so it needs to be set up in a well-ventilated room.
FDM: ABS, HIPS, PLA, composites, and more
Best used for creating functional prototypes, ABS stands for acrylonitrile butadiene styrene, a common thermoplastic famous – as well for its 3D printing-friendly properties – for being used to make LEGO bricks. Also known as filaments, these materials are essentially long strips of plastic that can be melted and extruded layer-by-layer into parts.
When heated to the right temperature, ABS is particularly easily shaped and hardened, making it perfectly suited to the production of toys, kitchen appliances, electronics, and other versatile plastic parts. It’s also toxic-free, chemical-resistant, lightweight, and durable.
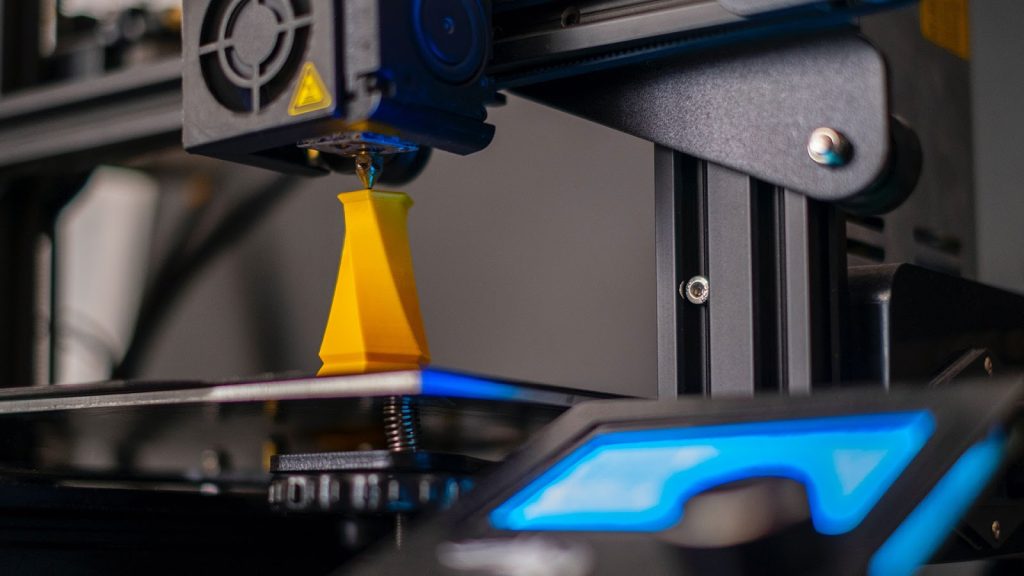
HIPS
Also known as high impact polystyrene, is a material commonly used with ABS as it serves as a dissolvable support structure. Just like its 3D printing companion, HIPS is lightweight and resistant, although it is cheaper and capable of withstanding much higher impacts. With d-limonene solution, it’s possible to rapidly remove HIPS support structures, something that’s a real benefit for those engaged in product prototyping.
PLA
Stands for polylactic acid, a thermoplastic made up of organic materials such as corn or sugarcane. Despite being a super effective filament, PLA isn’t that difficult to use, thus it has become a firm favorite among amateurs and professionals alike.
Unlike ABS, it is biodegradable and inexpensive, but it’s also weaker, less durable and not as heat resistant, which can result in parts being brittle. Thus, if you’re hoping to print anything that is supposed to be moved around, bent, or pulled, it’s worth opting for another material. Other than that, PLA is a reasonable-smelling, user-friendly filament, for creating objects with smooth, pleasant-to-touch finishes. Oh, and it comes in a very cool range of colors!
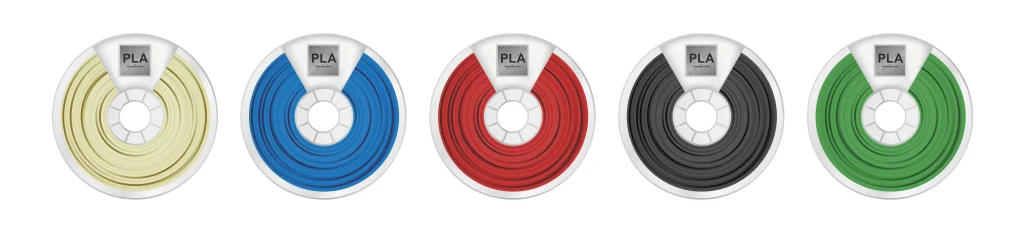
Composite materials
As the name suggests, are a combination of PLA, polyethylene (PET), nylon, and some particles or a variety of fibers, which reinforce the blend. In simple terms, composites mix at least two components, in a way that allows parts to be 3D printed with unique properties. By combining a thermoplastic with wood or metal particles, for instance, you can achieve a real wood look while reinforcing brittle fibers with alloys like kevlar.
Ceramic
May not be the first 3D printing material you’d think of, but they can safely be used to create solid objects of great durability and resistance, which are also aesthetically pleasing and pleasant to touch. Similarly to conventional pottery, these objects can also be kilned and glazed. Even though 3D printing is more commonly associated with resin or filament, ceramic has helped the technology branch out into the dental and architectural sectors.
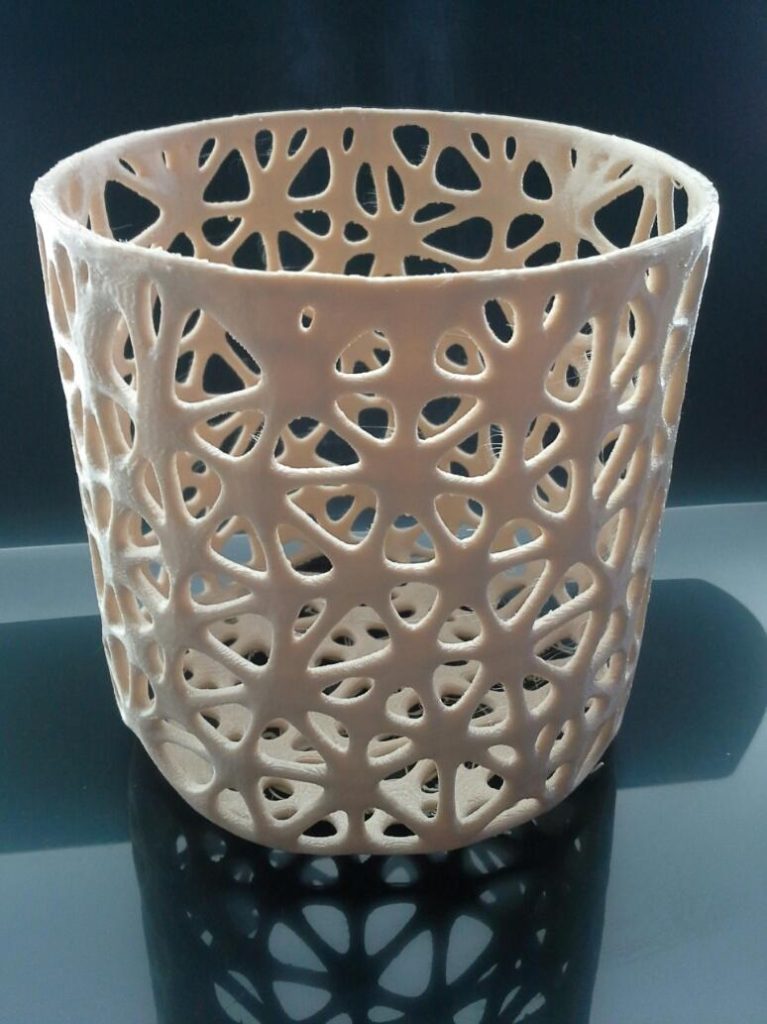
SLS: Nylon and TPU
Nylon
Otherwise known as polyamide, is commonly used in Selective Laser Sintering (SLS) 3D printing. Even though this group of synthetic polymers was initially created to replace silks, it now has use cases away from textiles, in the 3D printing of sturdy, complex industrial parts.
This material is tough, impact-resistant, and can easily withstand UV, heat, water, and chemicals. However, one thing to keep in mind is that nylon needs to be printed at temperatures of up to 250oC (482oF), so your system will need to support this!
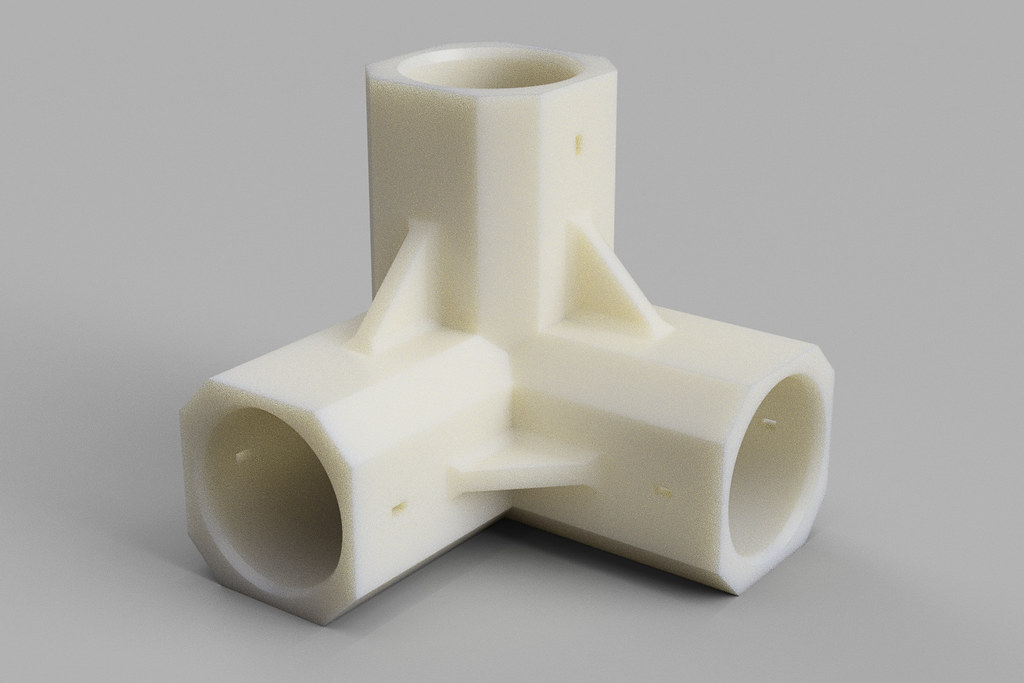
TPU, or thermoplastic polyurethane
Is arguably the most flexible filament of all. These elastomers are resistant to abrasion, grease, and oil, bend easily, and boast practically every property of rubber. TPU is also quite rigid and relatively easy to use. This accessibility and flexibility means that the material is used to create products as diverse as drive belts, inflatables, sporting equipment, medical devices, and footwear.
SLM and DMLS: metal powders
Metal powders most commonly used with selective laser melting (SLM) or direct metal laser sintering (DMLS) systems include copper, brass, bronze, and steel. While each of these tends to feature a different ratio of metal and binder, they’re all relatively heavy due to their metal content. Practically, they can either be used to create custom architectural pieces like little statuettes or sculptures with a metal sheen, or functional, lightweight alloy parts.
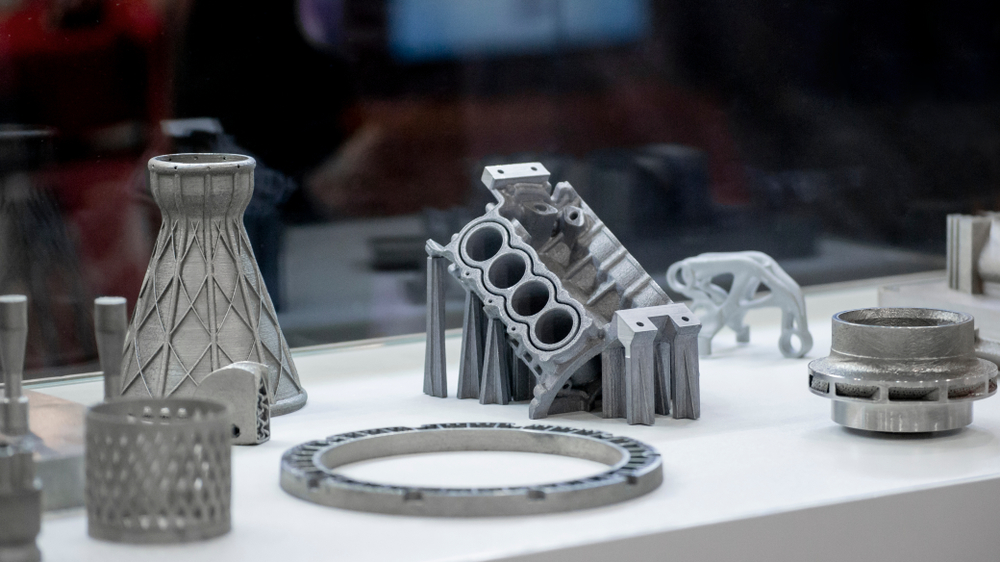
So, those are some guidelines to get you started. Needless to say, 3D printing materials are amazingly diverse, and each of the types described above could potentially be recategorized under several other headings, but here’s one tip: since getting into 3D printing could be a bit overwhelming, learn more about the types of 3D printing technology.
From there, once you choose, purchase or rent, and set up your 3D printer, you can decide which kind of materials to use – luckily, the current market has the coolest range of materials to offer. Have fun!
Interested in finding out more about the different kinds of 3D printing materials? Check out our in-depth follow up articles below: