With the tariffs introduced by US President Donald Trump making headlines around the world, people are understandably worried about the prospect of retaliation and economic decline.
However, it’s not all doom and gloom. 3D technology developers often tout their potential as on-shoring tools for producing goods and spares in-house. As manufacturers come to terms with Trump’s tariffs, many will be considering how to achieve this very thing. In this light, the post-tariff world may seem daunting, but it’s also a world of huge in-sourcing opportunities.
It’s too early to jump to conclusions about how long Trump’s tariffs will last, but there are plenty of reasons for manufacturers to retain a degree of optimism. From digital inventory to Industry 4.0 production lines, the technologies of tomorrow are fast becoming those of today.
Here are some of the best-explored, tariff-busting 3D technology use cases we’ve seen so far:
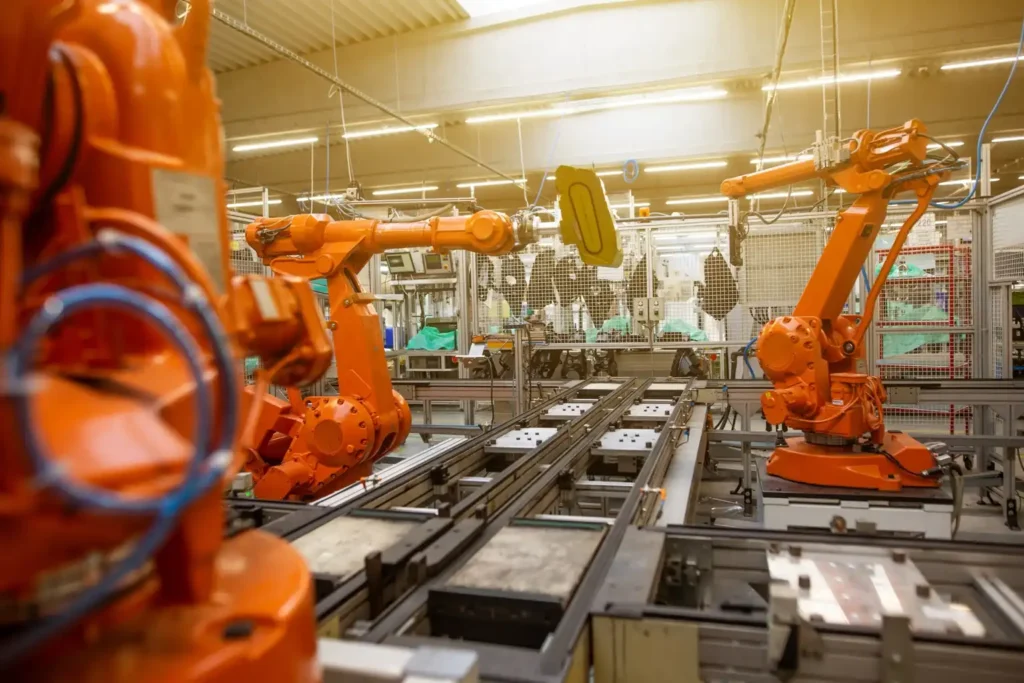
1. In-house manufacturing
From the outset, we should point out that 3D printing is no longer just a prototyping technology. Of course, it’s still widely used here, but the technology is also extremely effective at producing relatively small numbers of complex custom parts.
Jigs, fixtures, and tooling are some of the most commonly 3D printed parts currently deployed in industry, and there’s plenty of scope to apply the same principle elsewhere. As 3D technologies progress, this is only becoming easier. Take food-contact parts – those that can safely be used during food production, processing, or packaging.
Research carried out in labs like the Danish Technological Institute’s (DTI’s) has led to the advent of nylon, titanium, stainless steel, and aluminum 3D printed food-safe parts. With the right equipment (notably post-processing gear for sealing surfaces and avoiding contamination), manufacturers can theoretically make these parts in-house rather than ordering from a vendor.
Food-contact components are just a drop in an ocean of potential short-run 3D printing applications. If Trump’s tariffs stay in place (or worsen), manufacturers will surely look to fulfill more of their supply needs in-house, creating significant opportunities for the 3D industry.
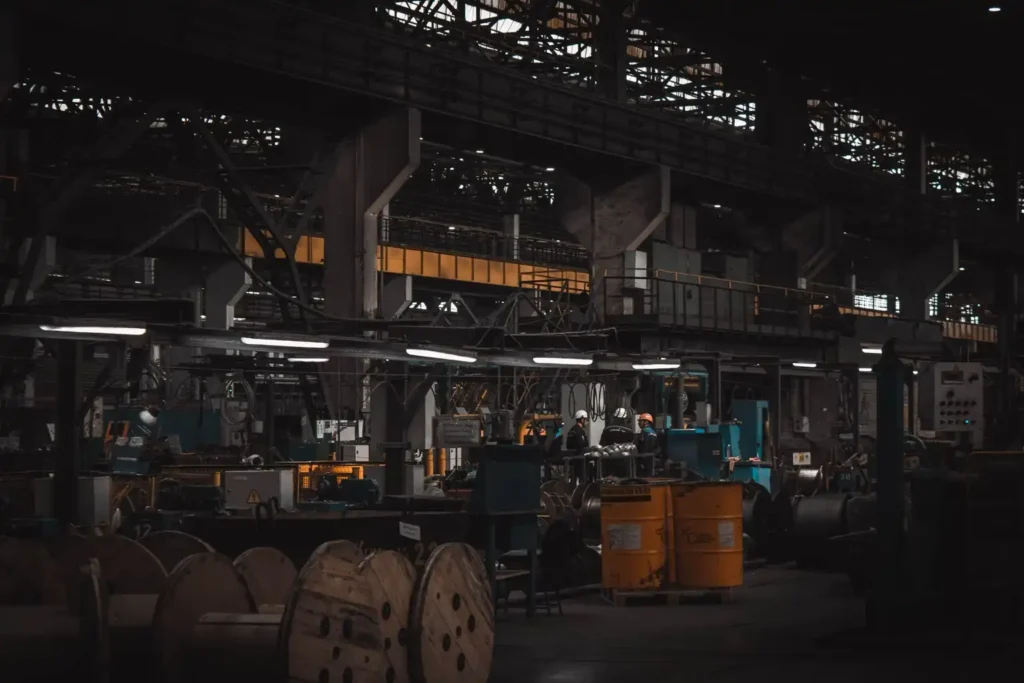
2. Rapid prototyping
We may have already mentioned prototyping, but it’s worth underlining the potential cost-savings companies can make by in-sourcing this kind of activity. Without their own 3D scanners or 3D printers, manufacturers either need to make a physical mock up or manually create a 3D model and send this to the service provider for production.
While service providers remain a solid option (especially if they’re domestically based), iterating upon new designs in-house offers significant cost and lead time benefits. Given that the latter plays a significant role in a product’s time to market, this should definitely capture the imagination of SME manufacturers – particularly for those constantly engaged in R&D.
Prototyping is a broad field, but to offer an example, many Formula 1 teams already use 3D printing extensively for aerodynamic R&D. If SLA technology can meet the fast-moving needs of the world’s most demanding motorsport, it can easily be used for everyday design.
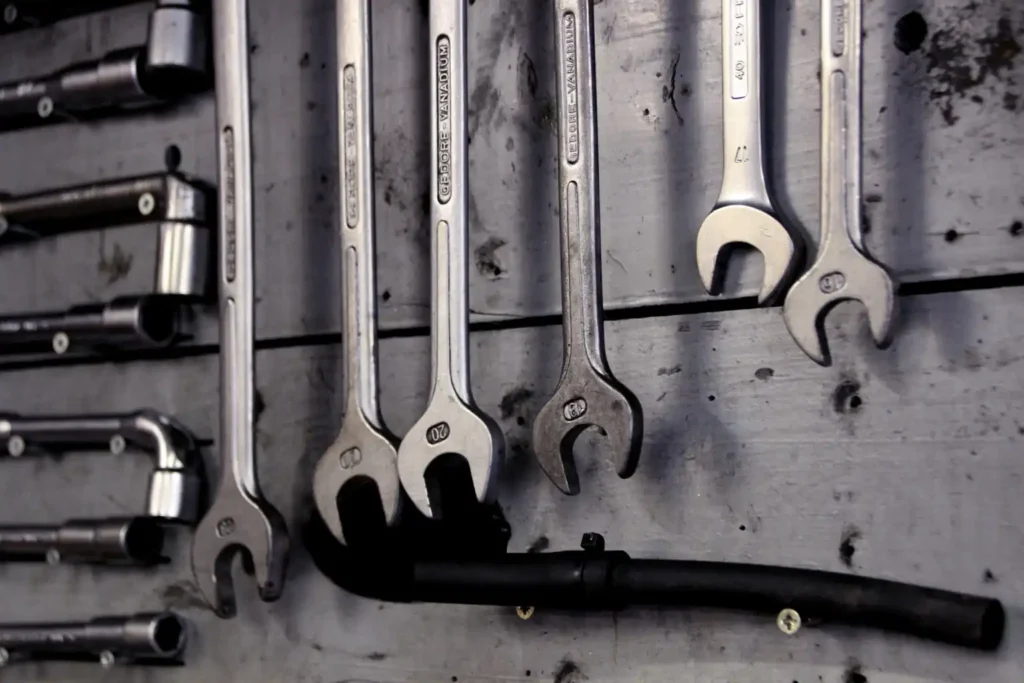
3. Digital warehousing
Another key aspect of on-shoring is ‘digital warehousing.’ Imagine only having to make spares on-demand. Not only would this save on warehouse costs, it’d drastically reduce any losses associated with part wastage – after all, you’d only make what you need, as you need it. This is especially attractive to those working in remote areas like oil & gas plants.
Sending parts out to refineries can take weeks and months. But digitizing them prior to breakage allows them to be manufactured as they’re required. This is where technologies like 3D scanning come in. High-accuracy and resolution 3D scan data offers the perfect basis for reverse engineering parts, as a means of storing designs or carrying out in-depth analysis.
At Team Inc., Artec Leo 3D scanning is used to conduct repairs on-site. Its engineers simply turn up at damaged pipelines, scan the affected geometries, and send measurements back to base. This data allows for the creation of custom pipe clamps that can be deployed during site operation, allowing for repairs to be carried out rapidly, without any costly delays.
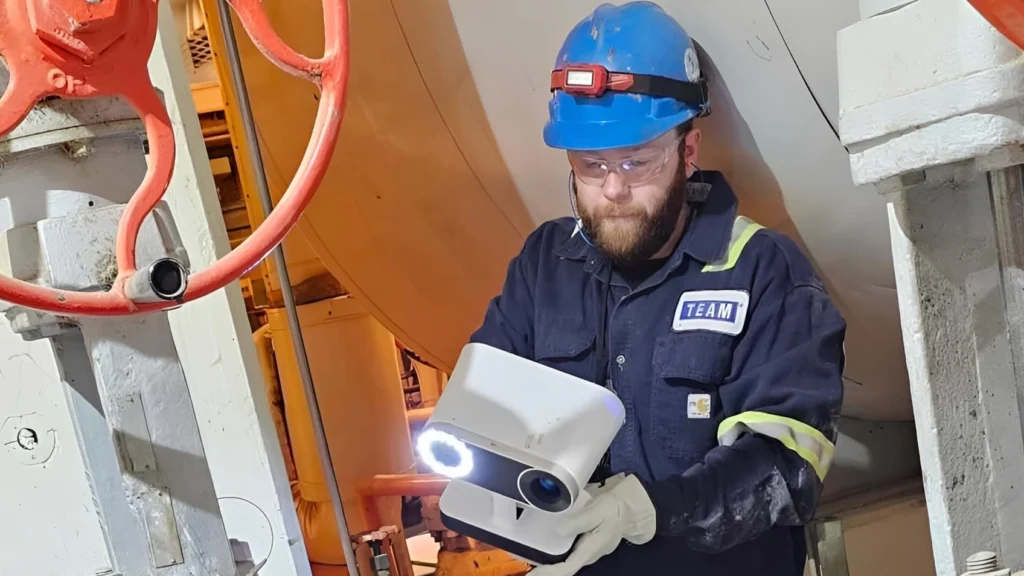
4. Aftermarket parts (and retrofitting)
Finally, no on-site 3D printing feature would be complete without a mention of aftermarket part manufacturing. Many automotive firms capture the geometries of existing car models using 3D scanning, then 3D print a mold or an actual modification, ready for finishing and fitting.
Take the team at US-based Tucci Hot Rods. Creating classic car modifications with physical templates previously took the company up to 20 hours each. With 3D technologies, its team can now modify in minutes, and address many more customers’ tuning needs in a single day.
Again, the concept of retrofitting isn’t exclusive to automotive. You could apply the same idea to any part that’s no longer in production. Digitizing such geometries allows them to be carefully examined to identify design intent – and even enables upgrades to the rarest of old items.
All of this will surely give manufacturers encouragement that they can find ways around President Trump’s tariffs. Discover more about digital warehousing in oil & gas here. Or find out how the global militaries are working on ways of 3D printing spares on-demand.